Improvement of solid motors and testing of recovery mechanisms
I have previously blogged about the N-2 rocket’s improved solid motors.
Since the aluminum combustion chamber melted in the recent test, the static test had to be conducted with the combustion chamber changed to mild steel. I was just in Japan on a business trip, but under the supervision of my colleague, the students were able to successfully conduct the test.
In the video above, the test stand is plodding along, and this was caused by the bulkhead coming loose from the rocket motor. The bulkhead came off because the groove in the combustion chamber that stops the snap ring to secure the bulkhead was too shallow. The following test was conducted to improve on this point.
The thrust curve is shown below, with a peak thrust of 514 N recorded. This time, the nozzle, not the bulkhead, was ejected, resulting in a rapid pressure drop. Next, the nozzle side was also tested with a deeper groove in the snap ring.
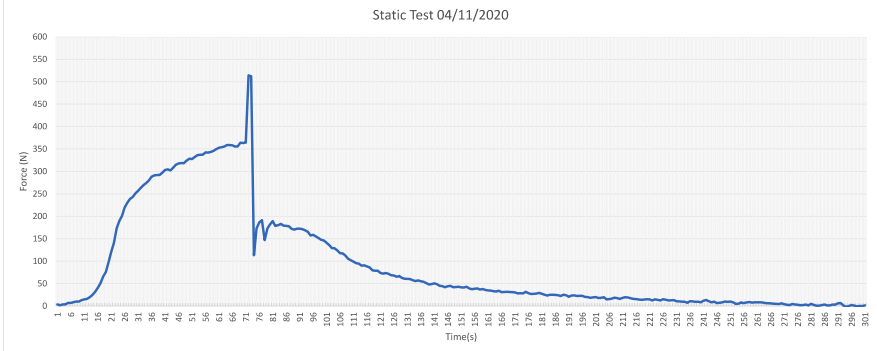
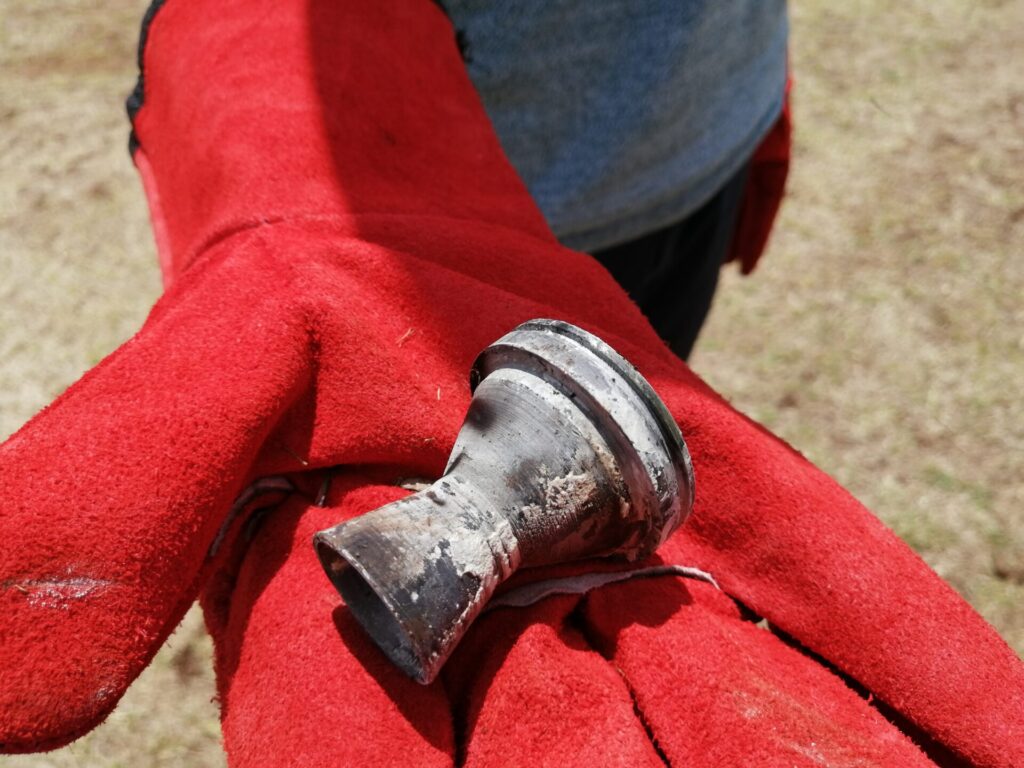
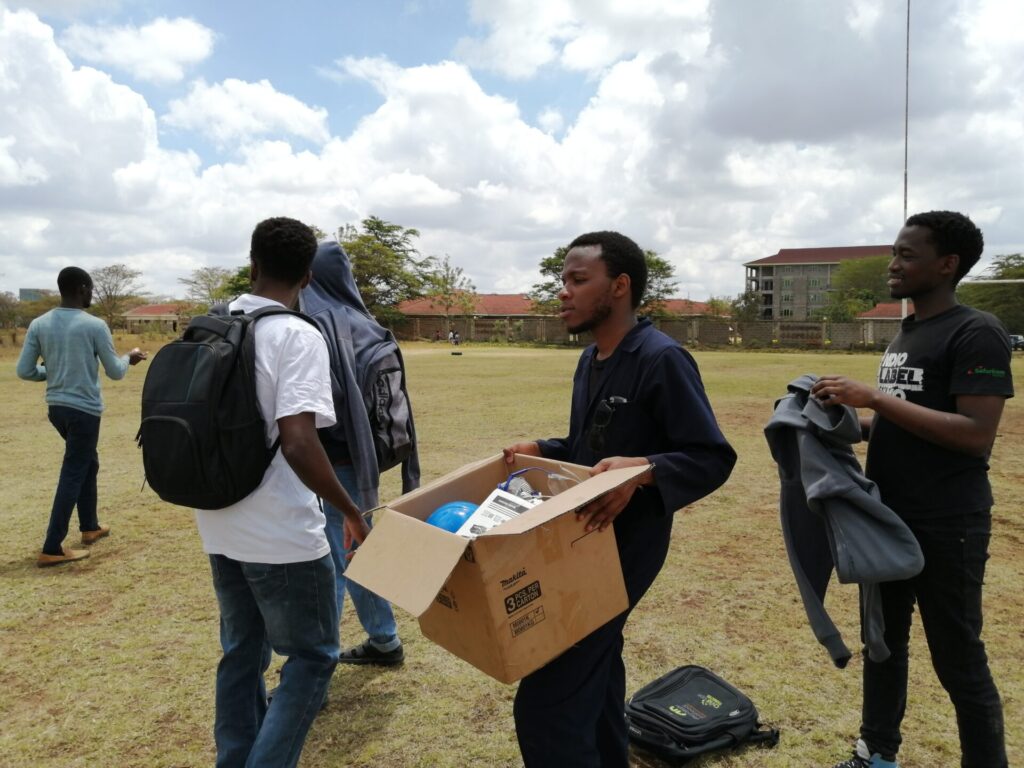
Now, in addition to the improvement of the solid motor, another important thing is the recovery mechanism, i.e., the recovery of the rocket by parachute. Unfortunately, the recovery by parachute has not been successful so far, and it is a long-cherished goal to achieve it in the next launch of the N-2 rocket. The ejection of the nosecone uses pyrotechnics, specifically an explosive called crimson powder.
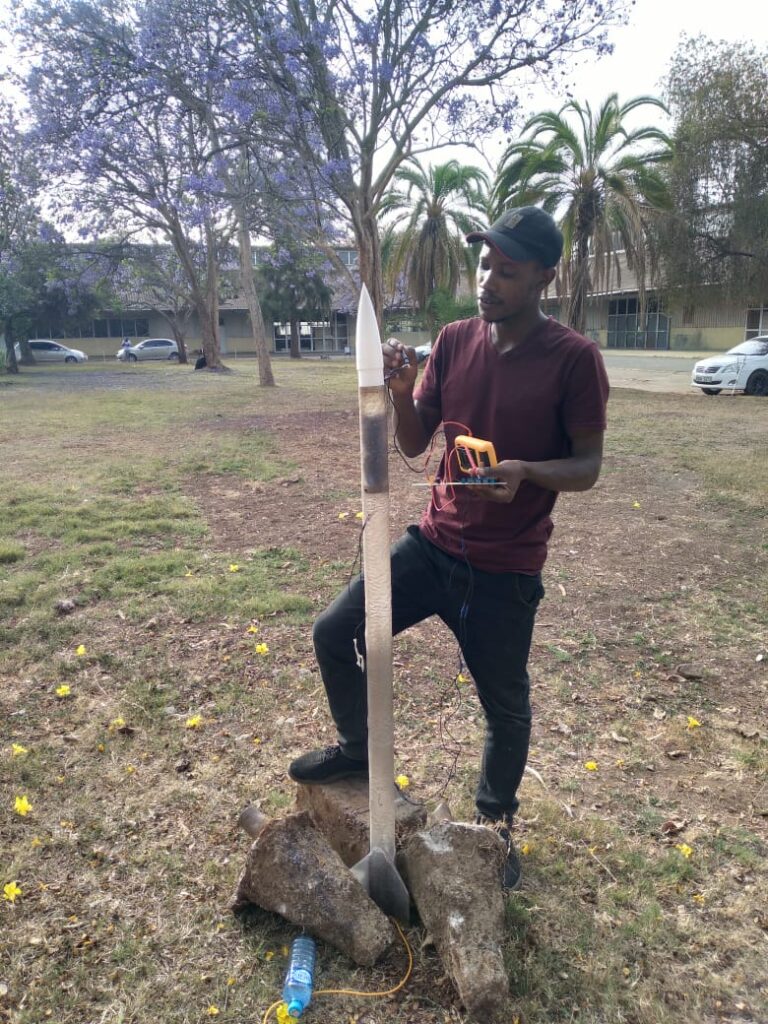
In addition, to test the control program (state machine) implemented in the flight controller, the team built a water rocket for the experiment.
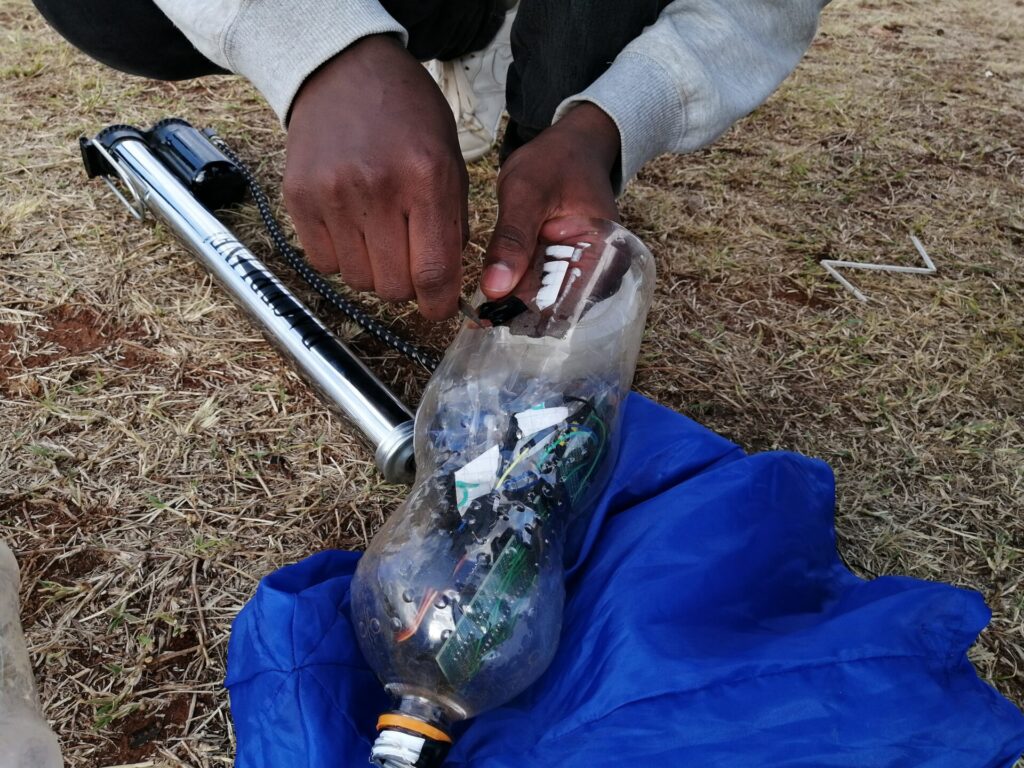
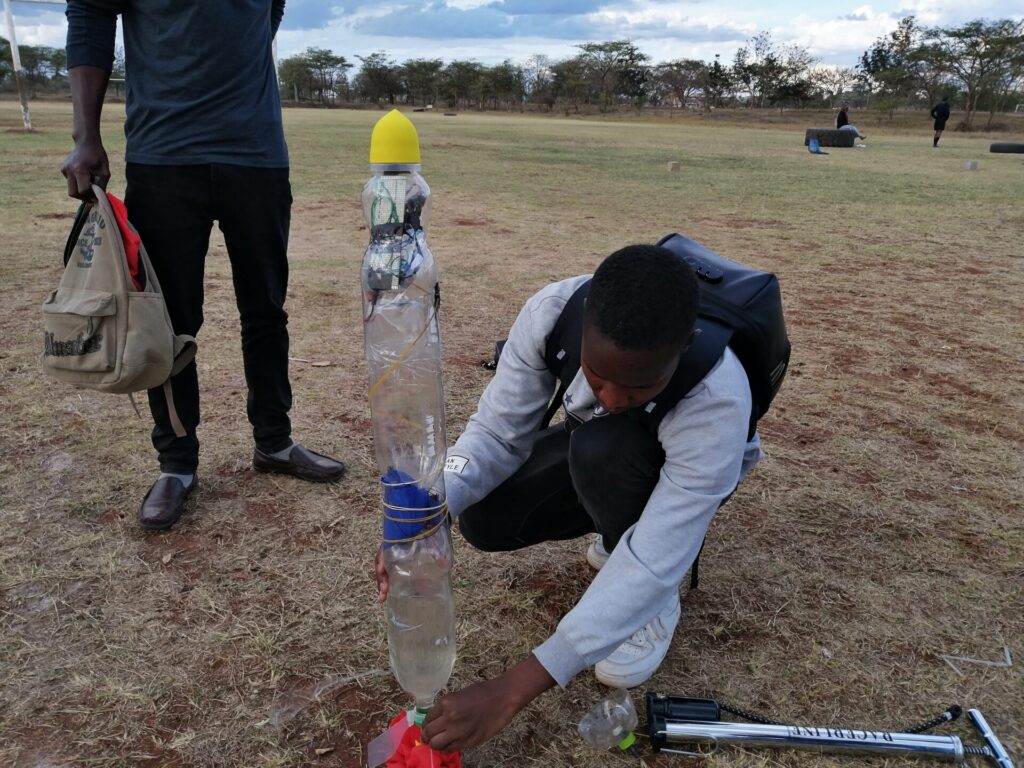
Water rocket launch (success)