Preparation for launch of N-3 rocket
The last article was about the launch of the N-2 rocket. Now I’m talking about the preparations for launching its successor, the N-3 rocket. It feels like a year has passed at warp speed.
The outline of the N-3 rocket is as follows. First, the target altitude is increased from 500 m to 2,000 m. The total length of the fuselage is 180 cm, and the diameter of the fuselage is 80 mm. The two types of materials were used for the fuselage: a fiberglass and an aluminum. The N-3 rocket has been redesigned to be more powerful in many ways. The N-3 rocket is taller than me, giving the impression that our rocket has grown far.
Later this month, we will launch five N-3 rockets named Simba, Chui, Kifaru, Tembo, and Nyati, in reference to Kenya’s BIG 5 animals. Although we started to prepare early, it is not easy to manufacture five rockets. We are preparing the components based on a manufacturing chart by considering what will be ready by what date. We are now digesting the tasks every day.
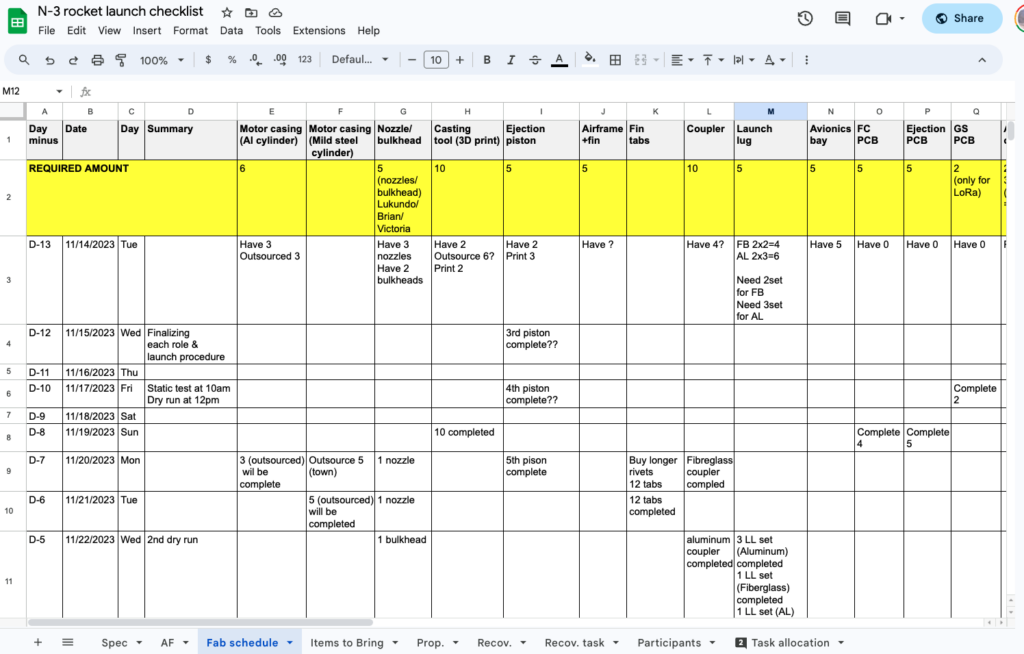
Especially time-consuming are 3D printing and metalworking. During this time of year in Kenya, it rains every day, and the 3D printing is frequently interrupted due to power outages. The 3D printer at home is in full operation almost around the clock. Since the 3D printer at the university also has a waiting list of students who are making their graduation projects, I outsourced a few parts to a local 3D printing service. The owner of the company told me that he is a graduate of JKUAT and attended a one-week digital fabrication course I offered on campus five years ago. After graduation, he started his own company related to electronic components. It is my pleasure to know that I was able to make a difference in the life of a young Kenyan.
The metal fabrication is also a lot of work: the solid rocket motor casing, bulkhead, and nozzle. The casing is 500 mm long, so boring the casing on a lathe takes time. Since it would be too time-consuming to manufacture all the parts by the students, I went to a fabricator in Nairobi introduced by one of our Nakuja alumnus.
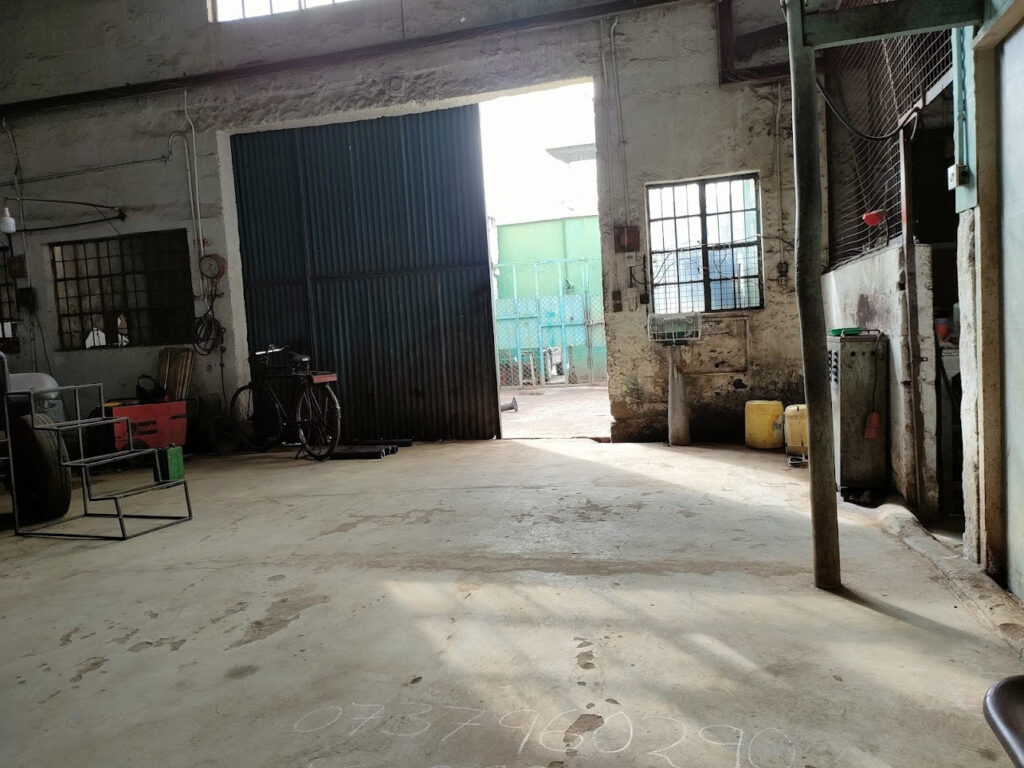
The solid rocket motor casing was switched to mild steel after a static test. Similar to the N-2 rocket, it was revealed the aluminum casing would not hold up to the heat. The next generation N-4 is also expected to have no choice but to utilize mild steel for the casing.
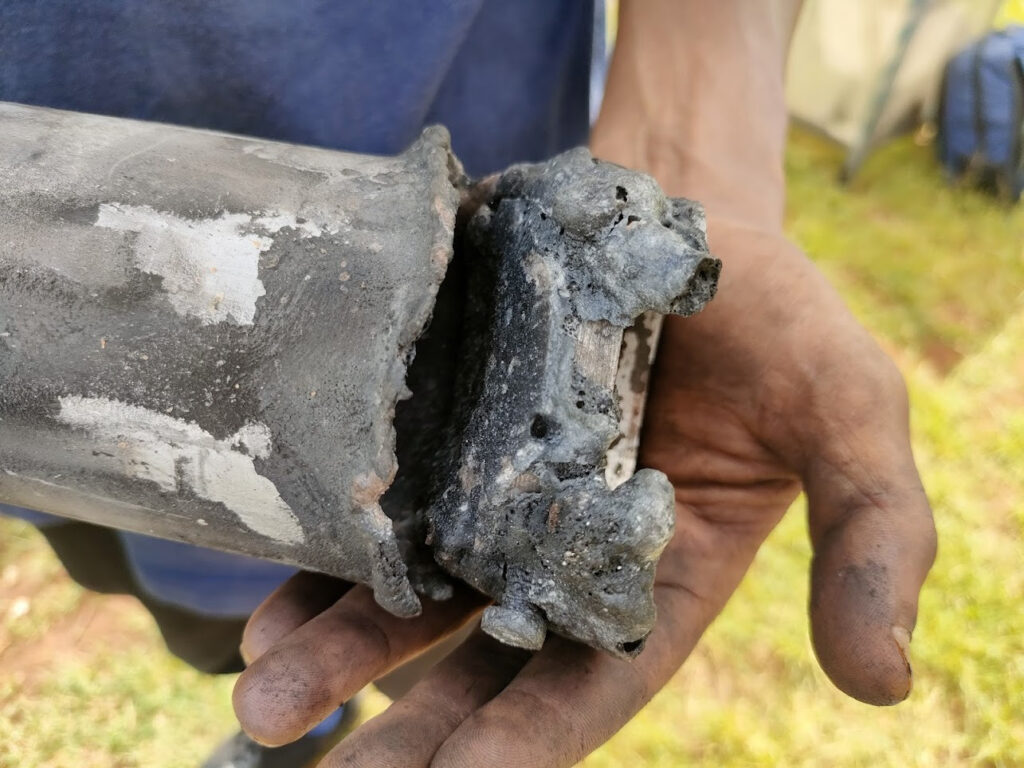
We prepared an antenna stand for this launch. This is because we made the mistake of forgetting to place the antenna on the ground during the launch of the N-2 rocket.
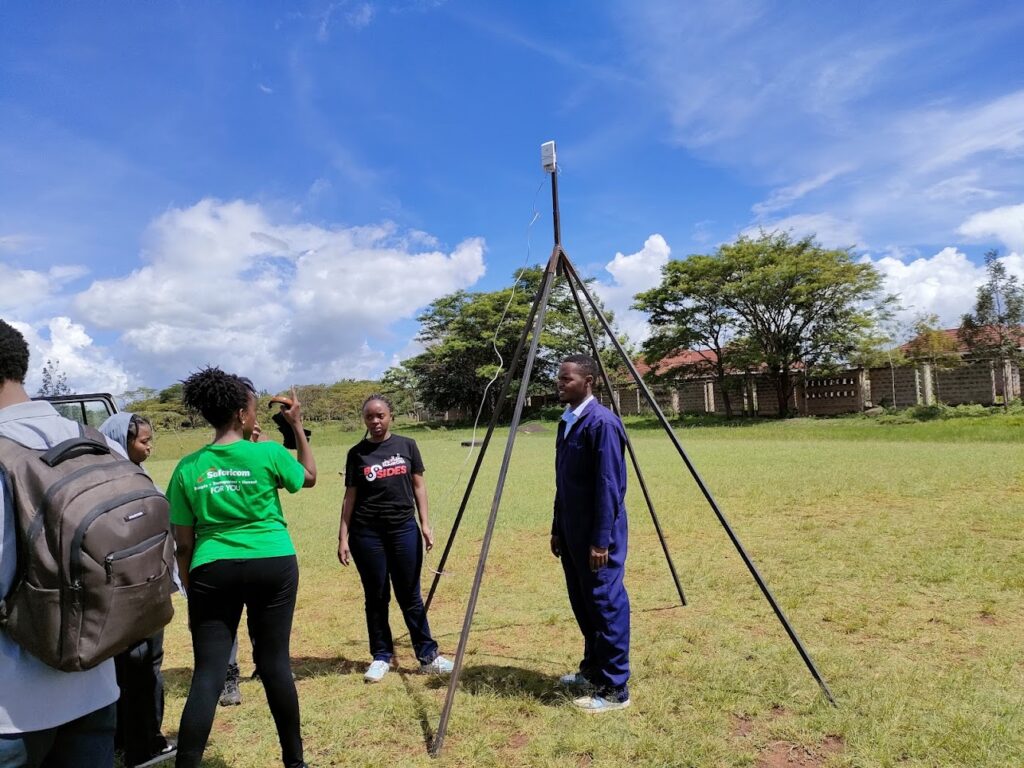
In the previous launch, it took time to prepare each rocket on site since we didn’t rehearse the process in advance. Based on this reflection, a rehearsal (dry run) was held to confirm the roles of each person and the preparation flow.
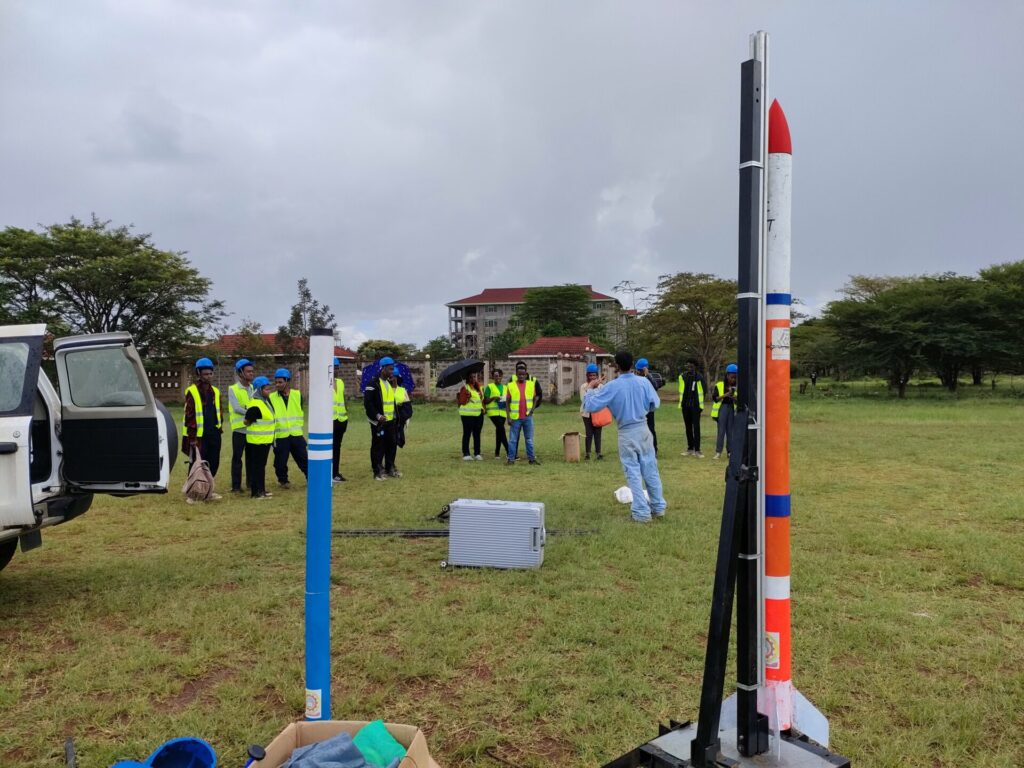
The students start working in the afternoon once they finish their classes in the morning. Every day seems like a carnival as the entire team working together everywhere. The marathon continues with just a few more days left before the main event next week.
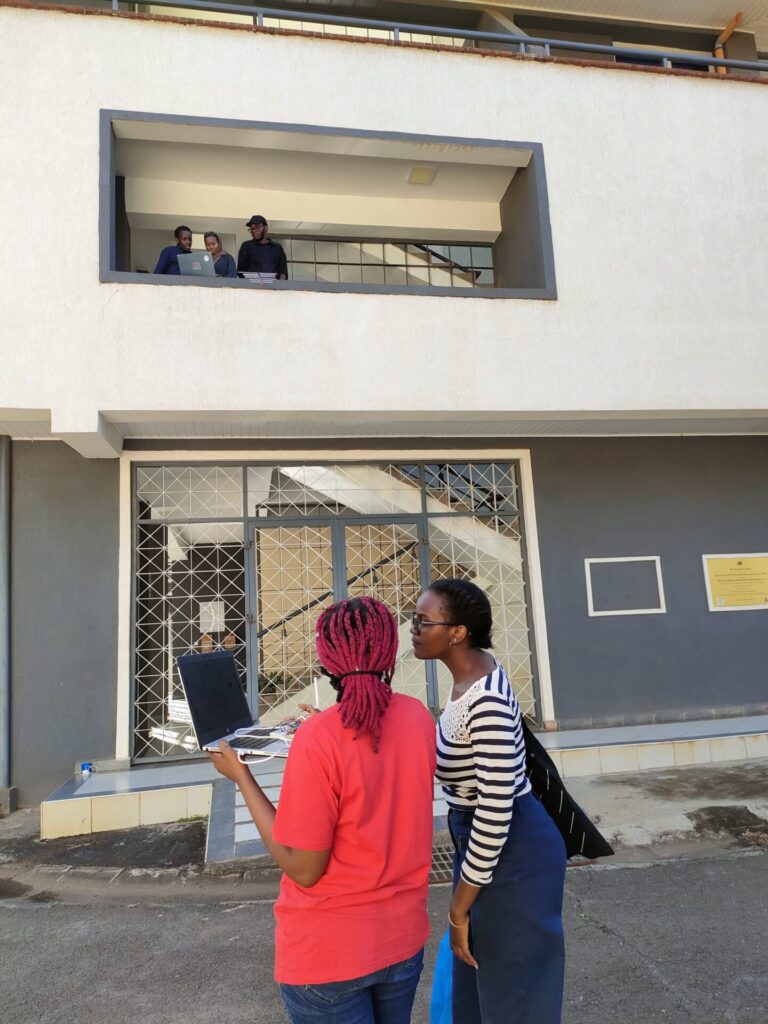
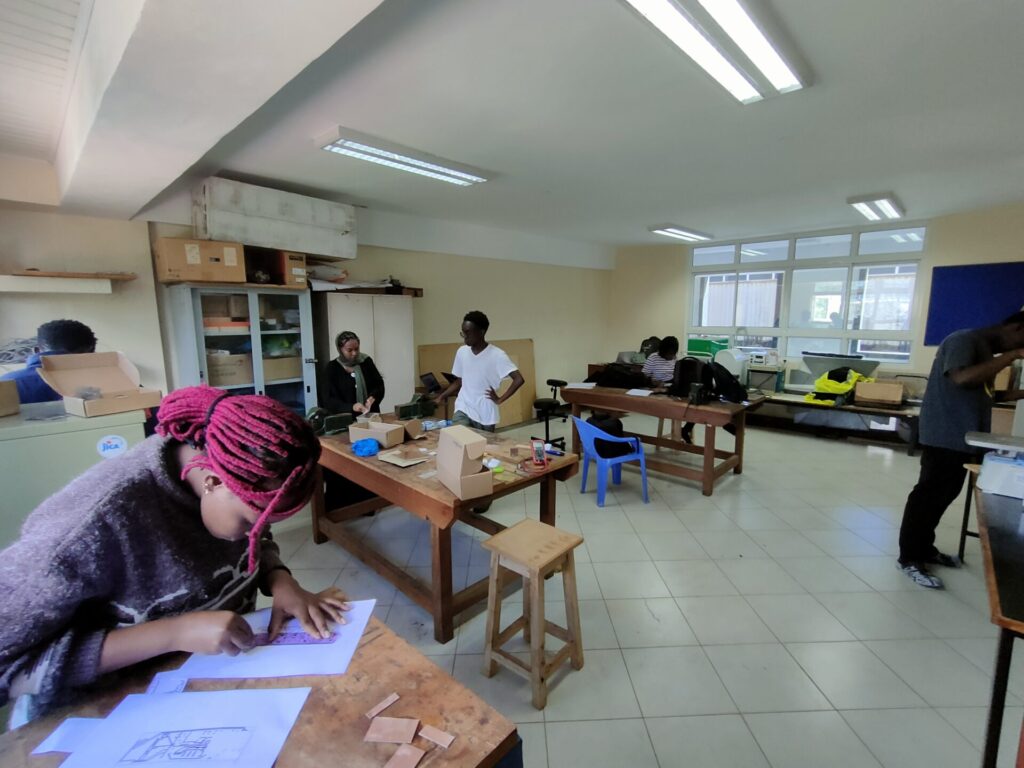
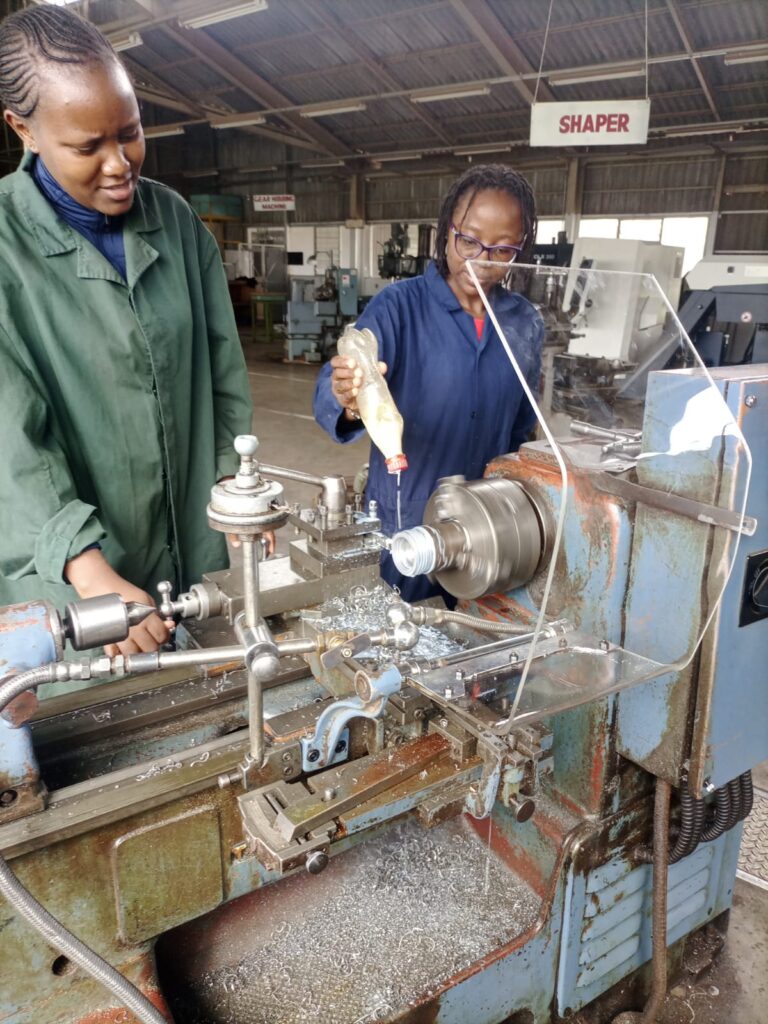