Ask advice from an expert: improving fiberglass manufacturing
Two events were scheduled for today. The first was a static test of the N-2 rocket motor. In the previous test, the nozzle could not withstand the pressure increase and popped out, so two improvements were made to the test: the groove depth was increased and the snap ring was doubled.
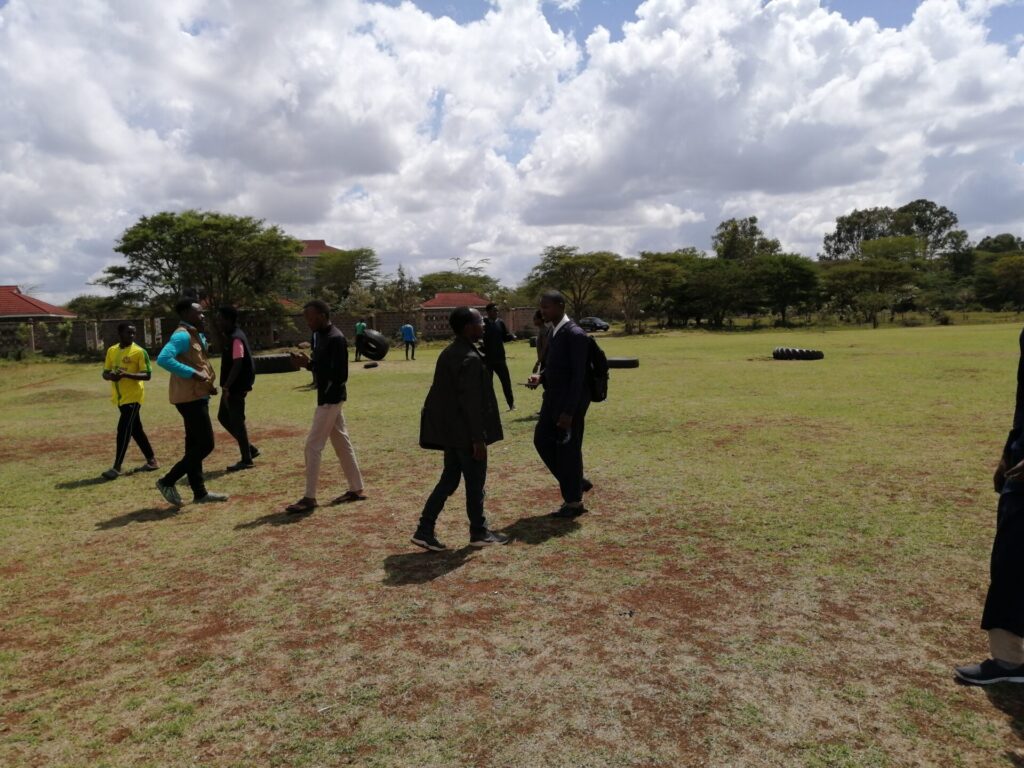
As it turns out, today’s test was not conducted. The reason was that there was a problem with the igniter. Since we had not prepared a spare igniter, we had to conduct two tests including this motor in the next test.
In the afternoon, we invited a fiberglass expert to JKUAT to teach us how to fabricate fiberglass airframes. He had originally worked for vehicle industry, where he learned fiberglass manufacturing.
When we showed them the tools we were using, he gave us the following advice immediately.
- Use a Fiber cloth (for the outer layer) or Tissue mat (for the inner layer) instead of a Glass mat
- Use a 2-inch paintbrush instead of a roller
- Use epoxy resin instead of polyester resin
- Use mirror graze polish (looks like vaseline) when removing from the mold
- Use aluminum for body tube molds, not PVC resin
- Use gelcoat for the final layer
The students, who had been engaged in fiberglass production by trial and error, listened to the opinions of the professional.
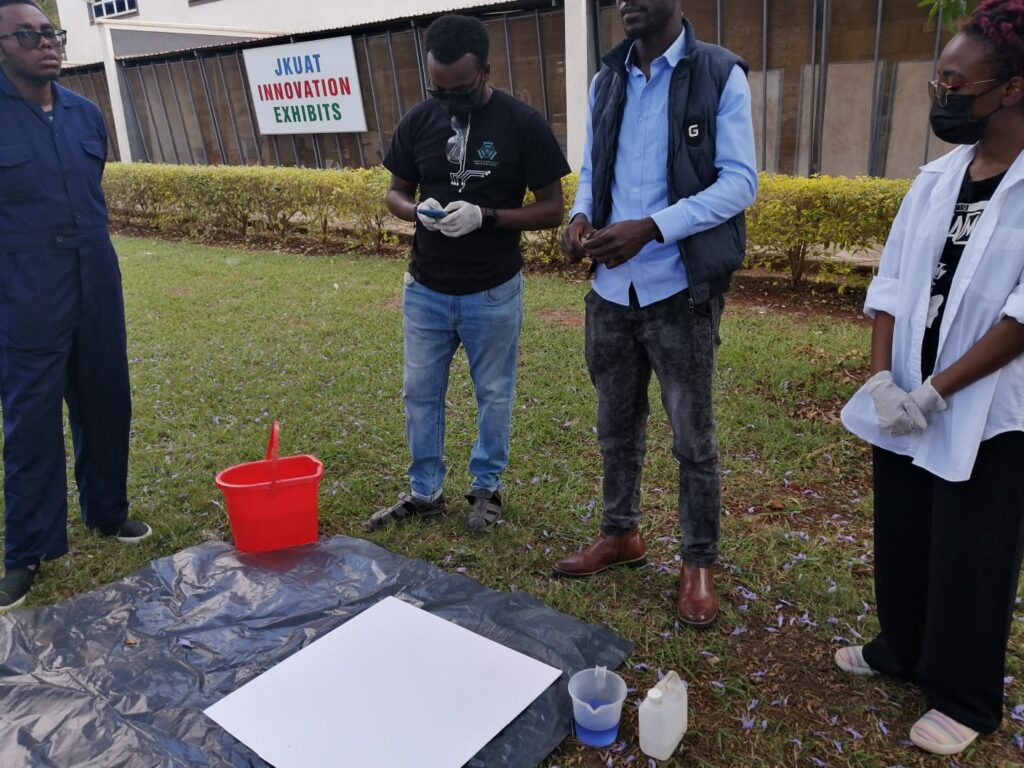
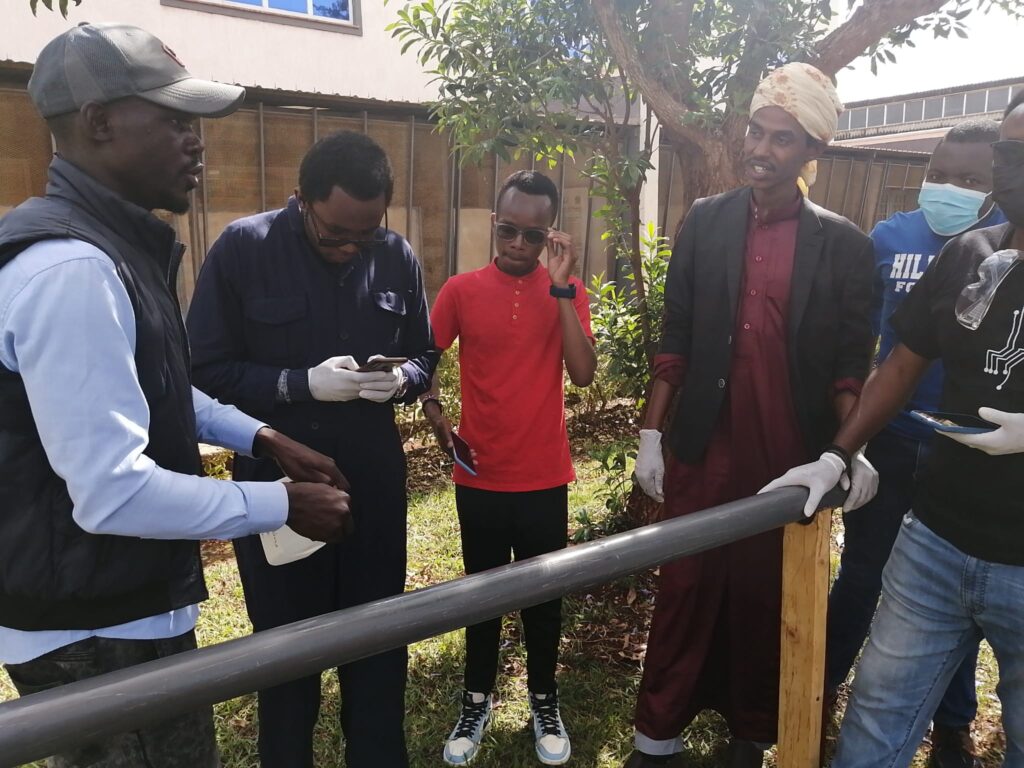
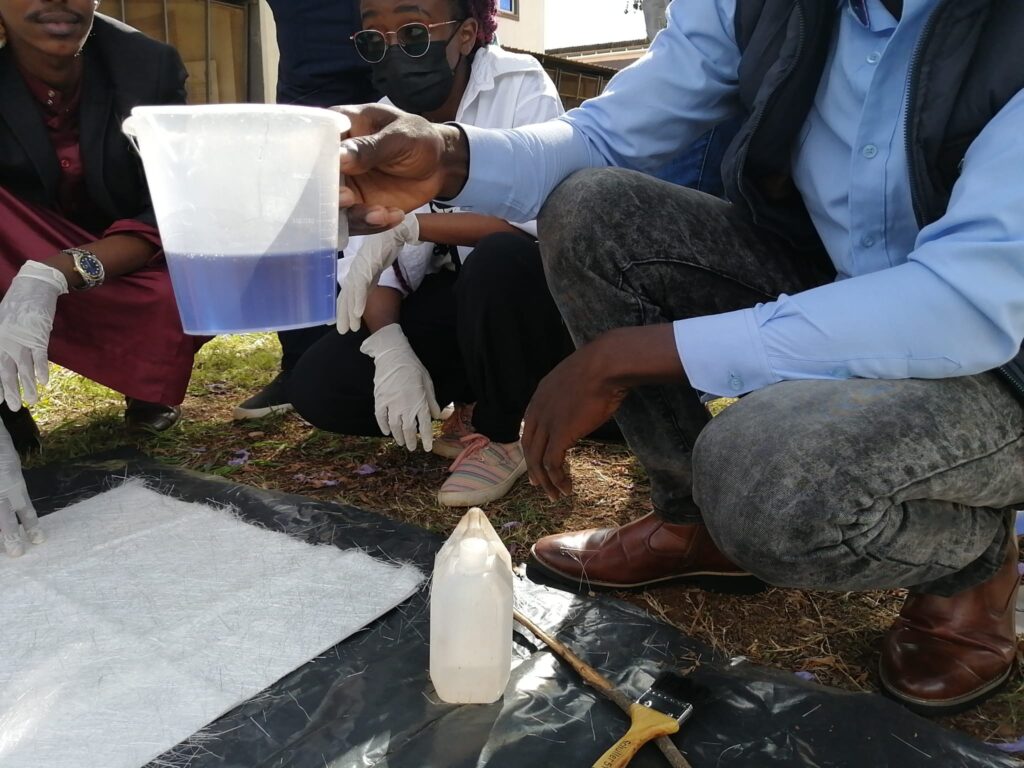
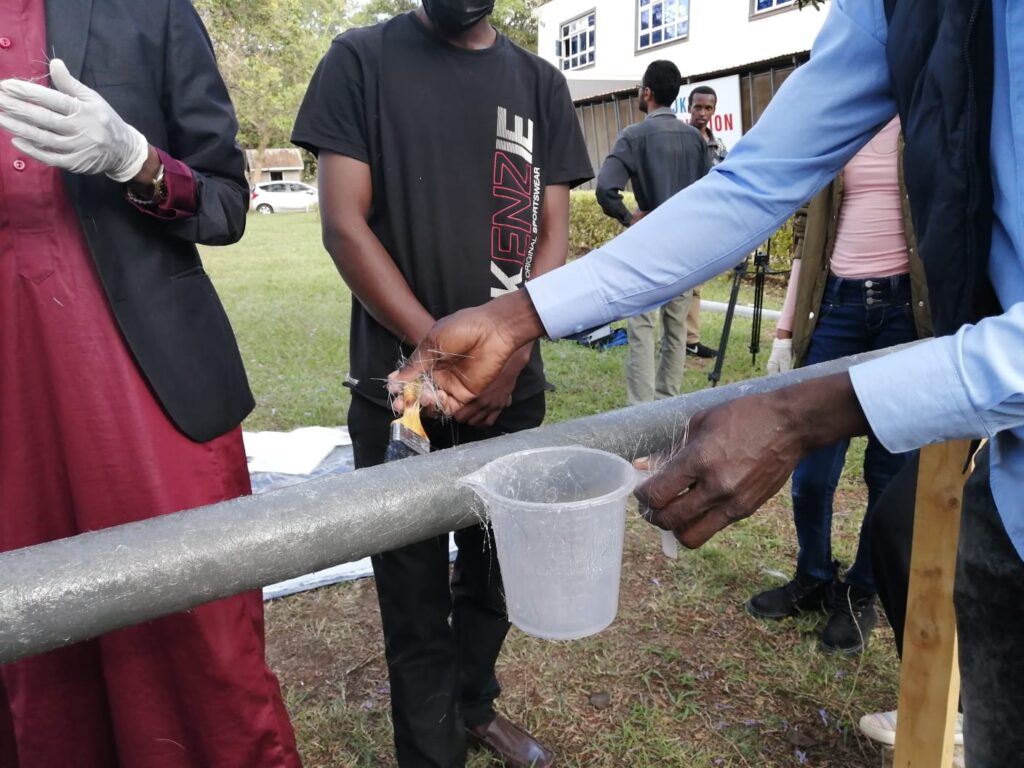
Today was also a day of progress for all teams, as the boards ordered from JLCPCB arrived.
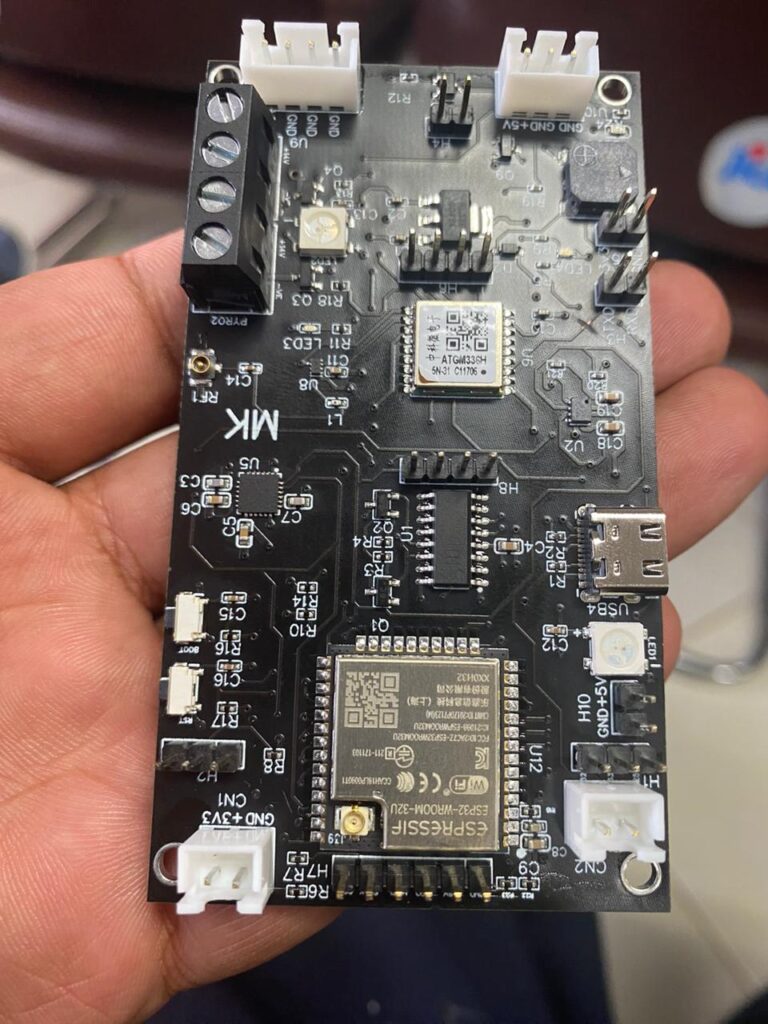