Ask advice from an expert: improving fiberglass manufacturing
Two events were scheduled for today. The first was a static test of the N-2 rocket motor. In the previous test, the nozzle could not withstand the pressure increase and popped out, so two improvements were made to the test: the groove depth was increased and the snap ring was doubled.
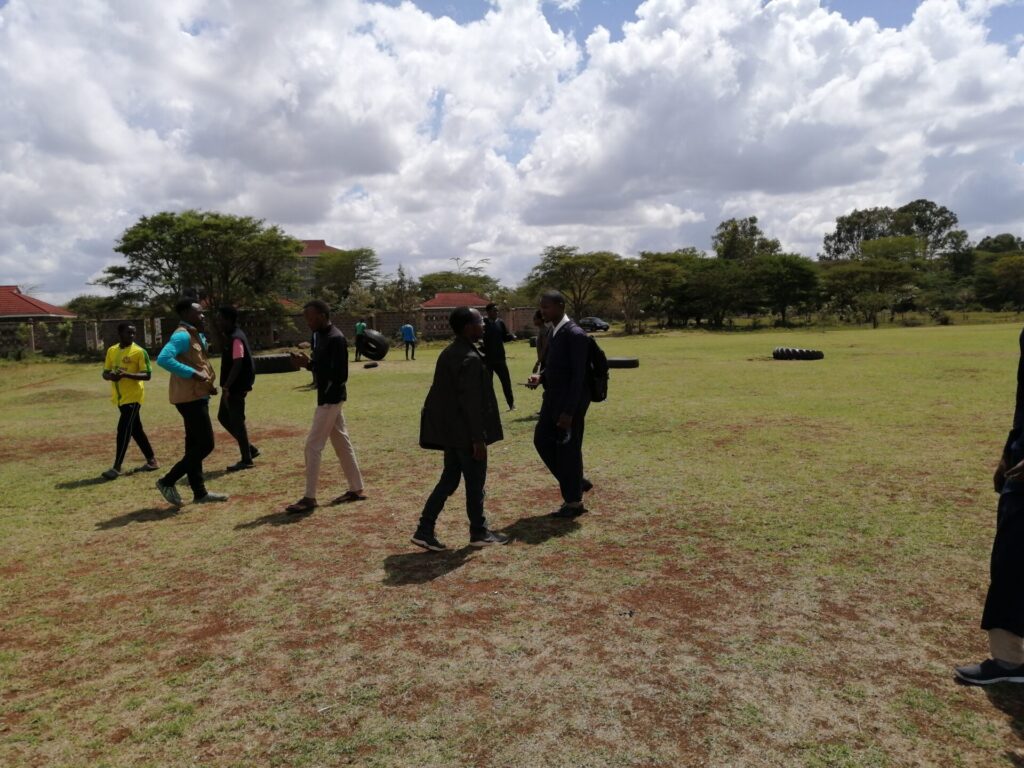
As it turns out, today’s test was not conducted. The reason was that there was a problem with the igniter. Since we had not prepared a spare igniter, we had to conduct two tests including this motor in the next test.
In the afternoon, we invited a fiberglass expert to JKUAT to teach us how to fabricate fiberglass airframes. He had originally worked for vehicle industry, where he learned fiberglass manufacturing.
When we showed them the tools we were using, he gave us the following advice immediately.
- Use a Fiber cloth (for the outer layer) or Tissue mat (for the inner layer) instead of a Glass mat
- Use a 2-inch paintbrush instead of a roller
- Use epoxy resin instead of polyester resin
- Use mirror graze polish (looks like vaseline) when removing from the mold
- Use aluminum for body tube molds, not PVC resin
- Use gelcoat for the final layer
The students, who had been engaged in fiberglass production by trial and error, listened to the opinions of the professional.
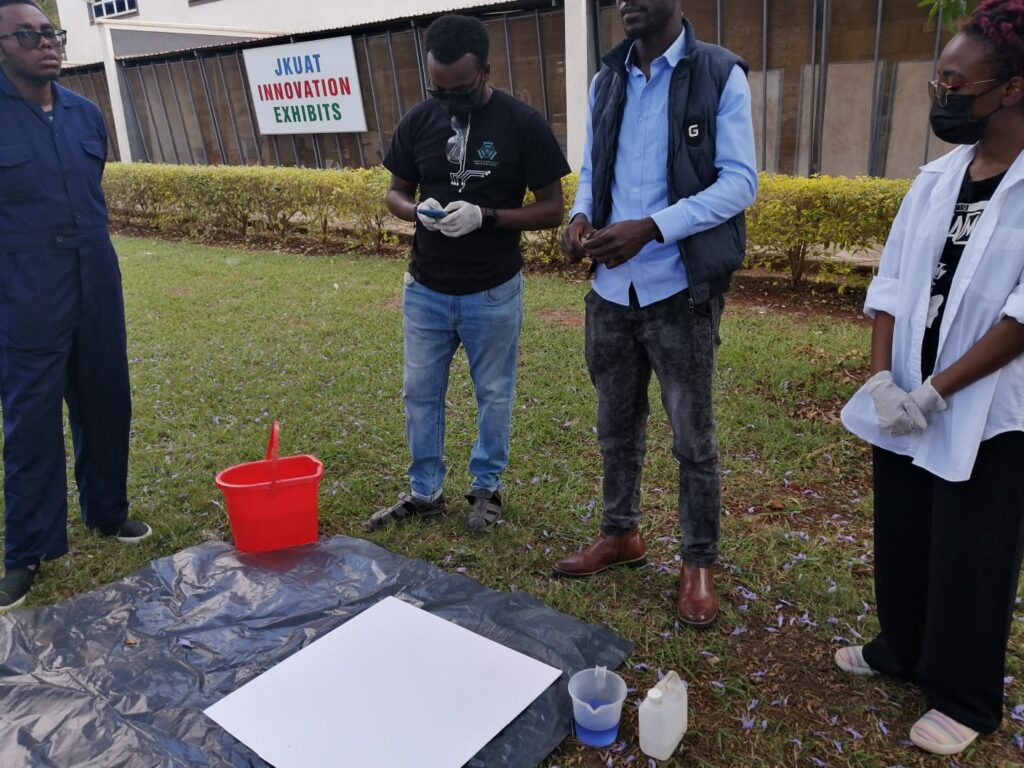
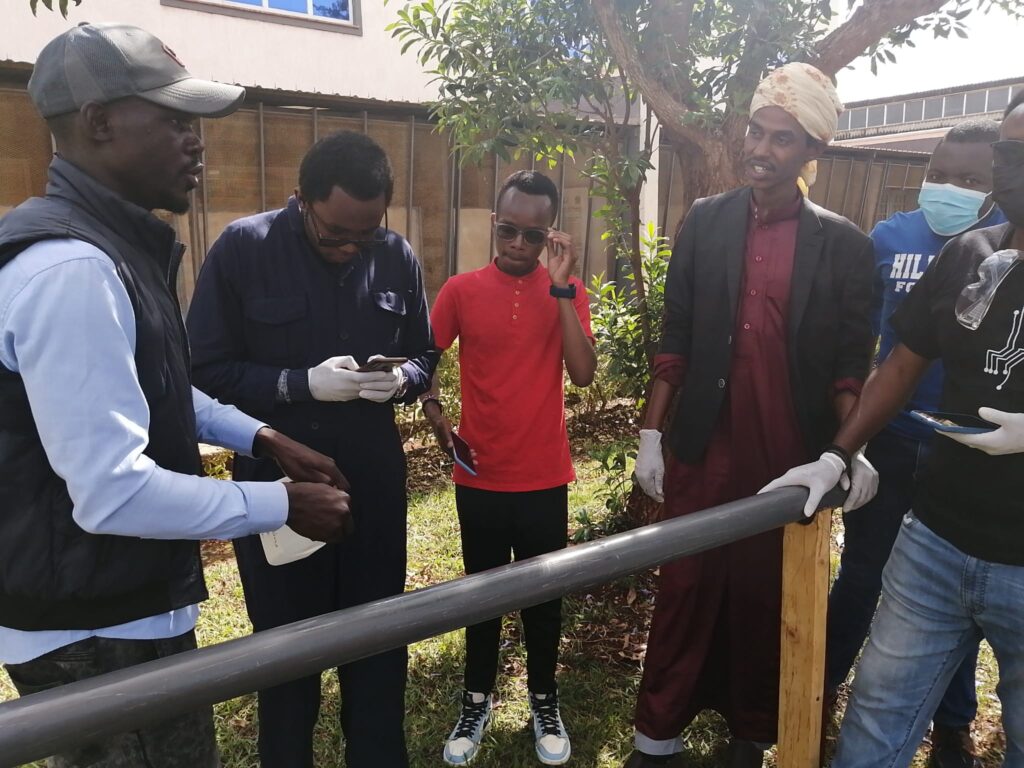
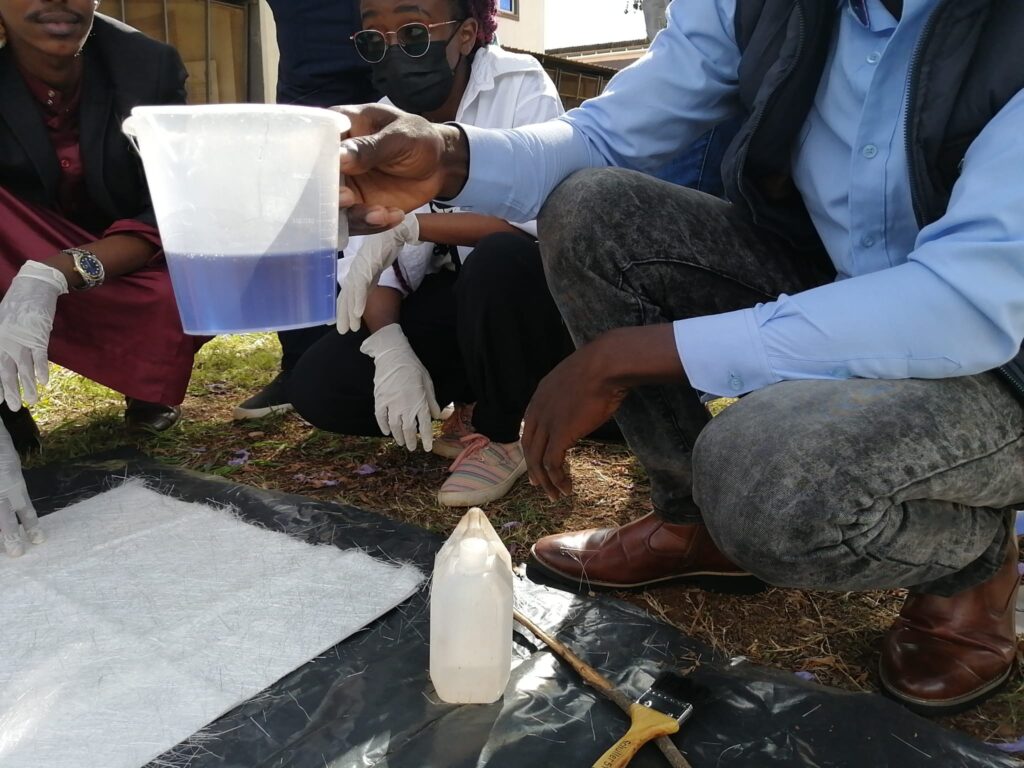
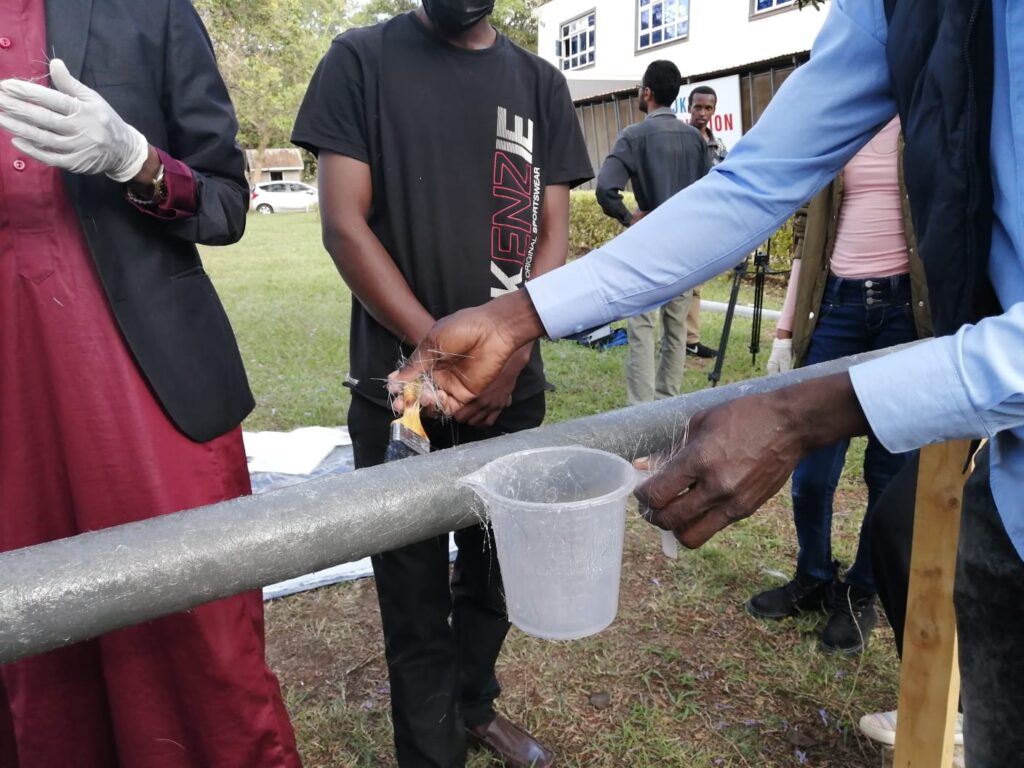
Today was also a day of progress for all teams, as the boards ordered from JLCPCB arrived.
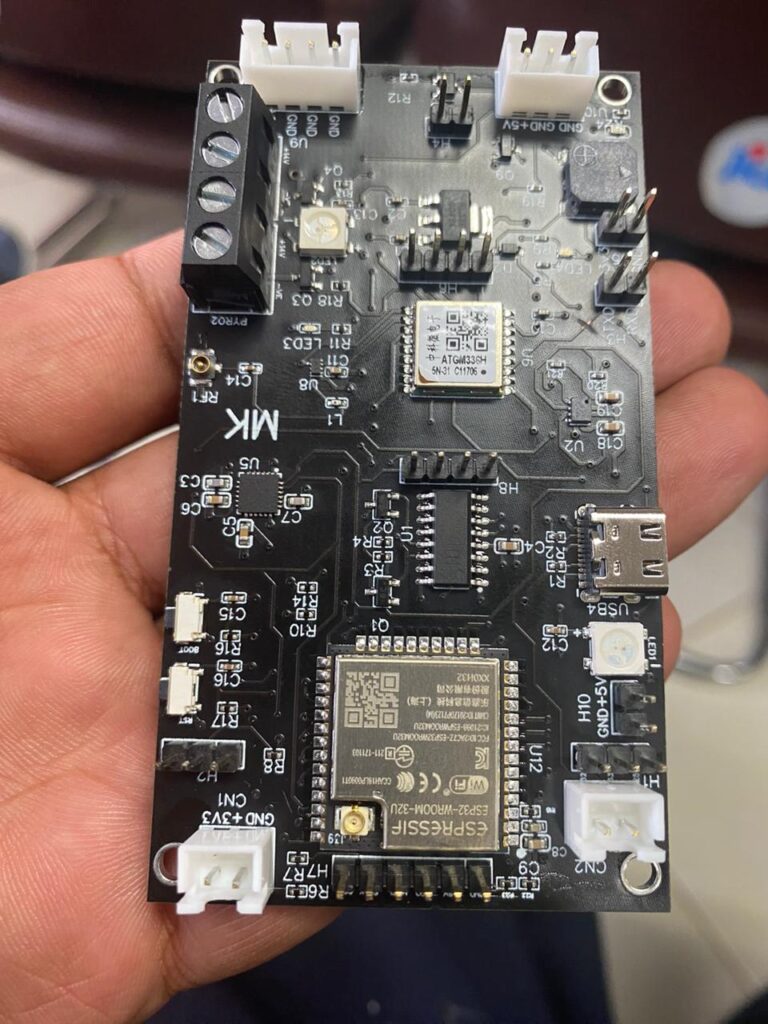
Communication test between flight computer and ground station
Today, the avionics team was conducting a communication test of the ground station at JKUAT’s farm.
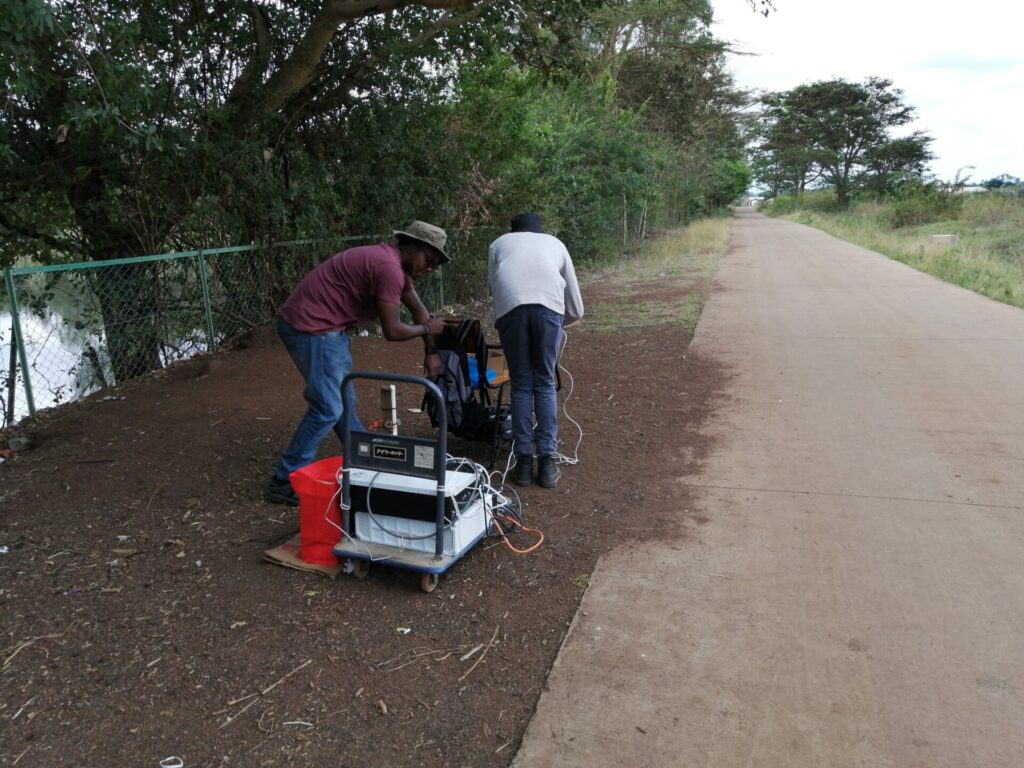
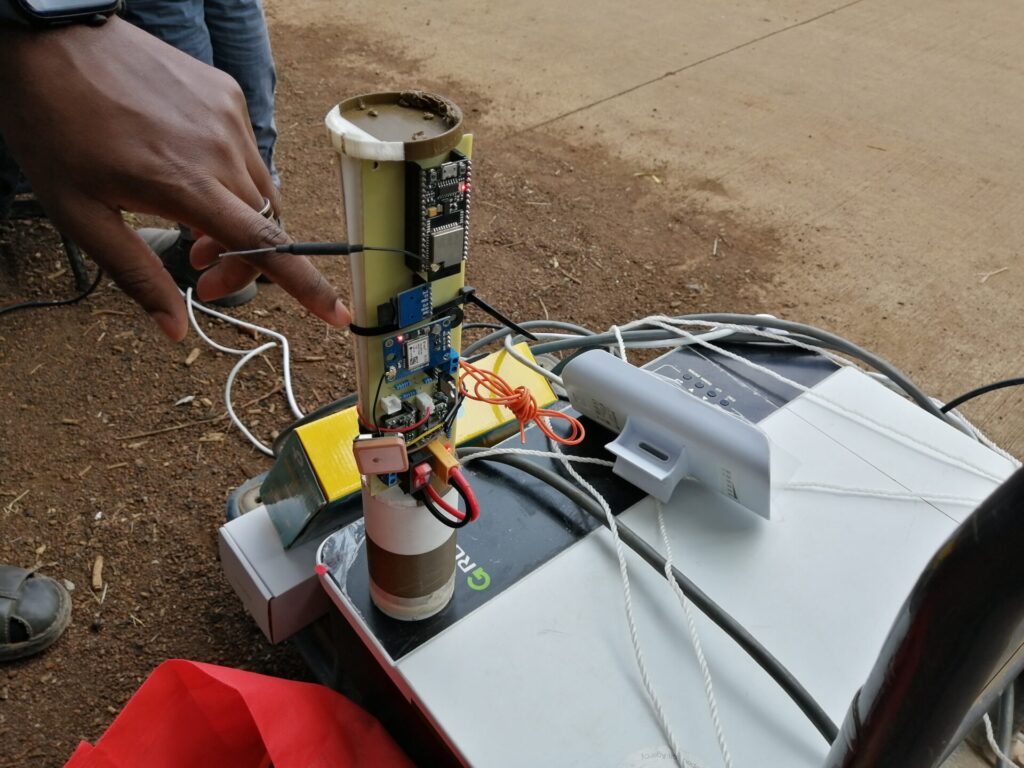
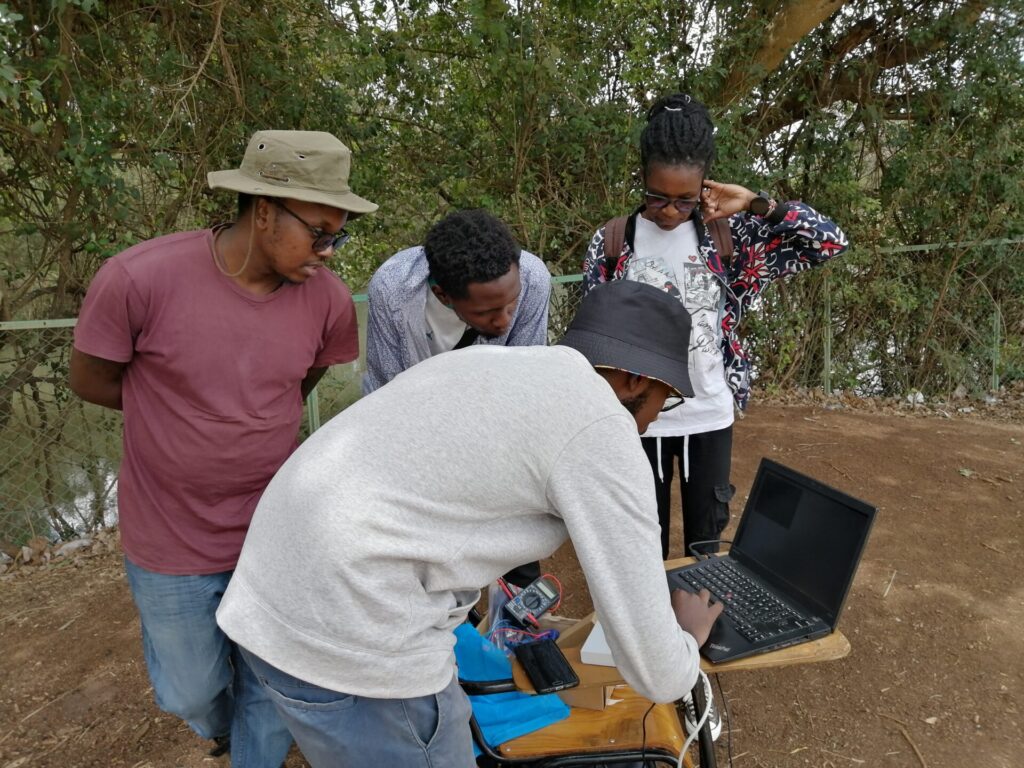
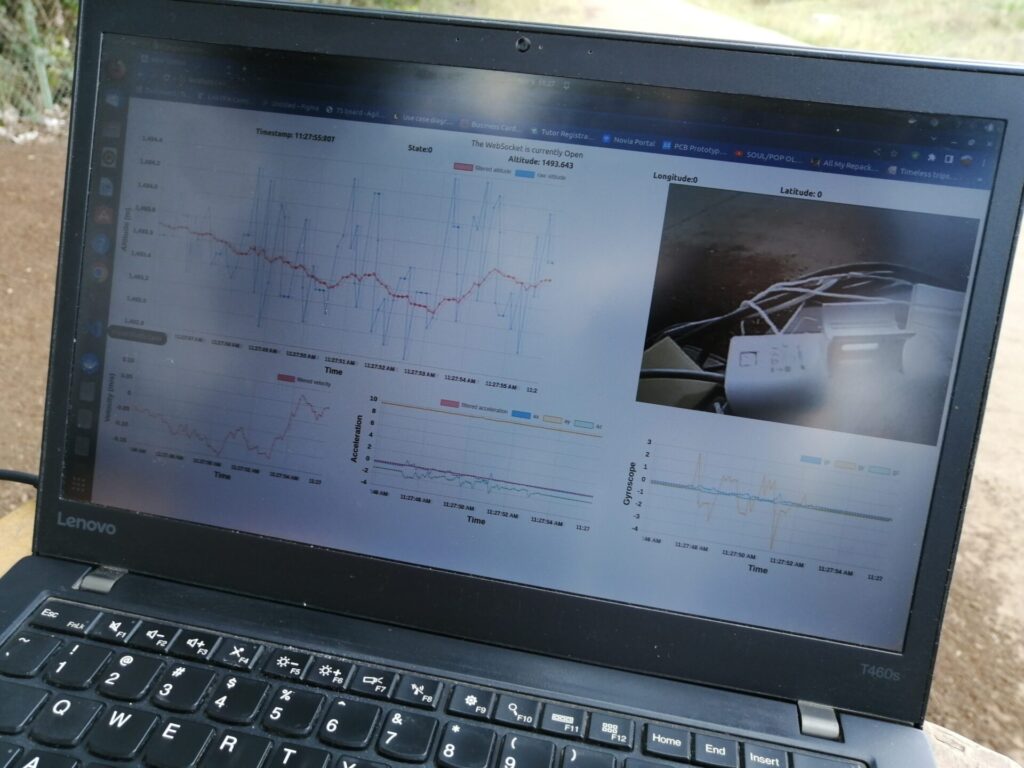
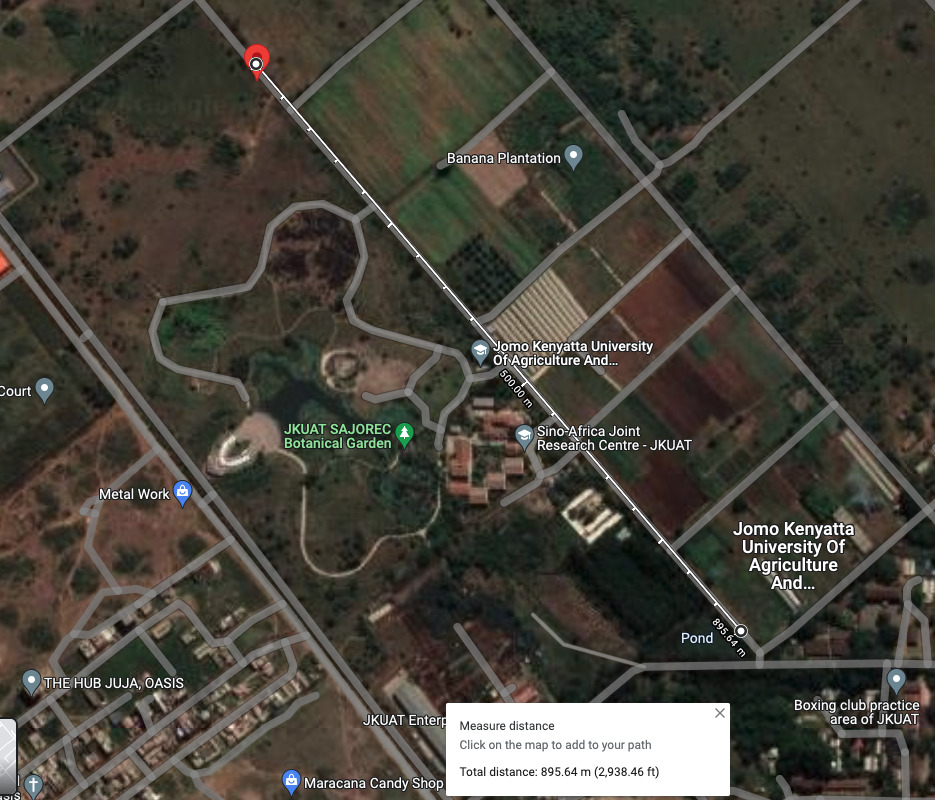
N-2 rocket body fabrication
Today the airframe team was building the fiberglass rocket body.
First, a sheet of polyethylene is wrapped around the PVC tubes (one 56 mm and two 75 mm) that will serve as the mold. This was done to make it easier to pull the cured fiberglass out of the mold. The students initially used polyethylene sheets, but the wrinkles in the polyethylene sheets adversely affected the dimensions of the final product, so they explored other methods (such as using a cling film). In the end, none of the methods worked, and they came back to the first method.
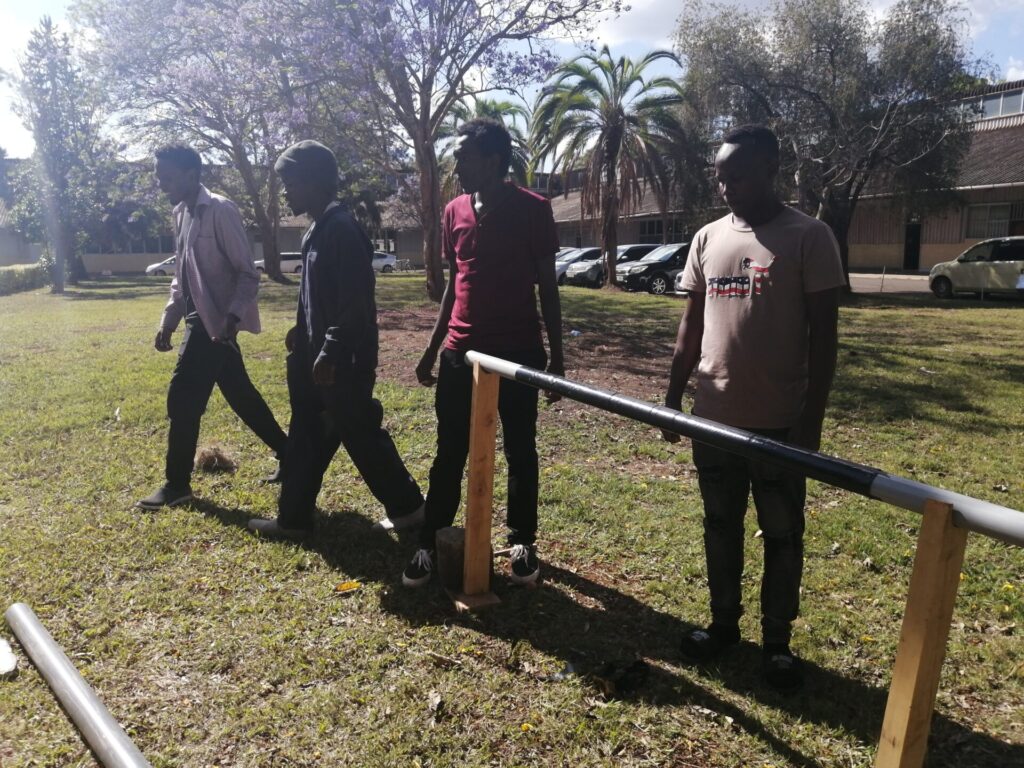
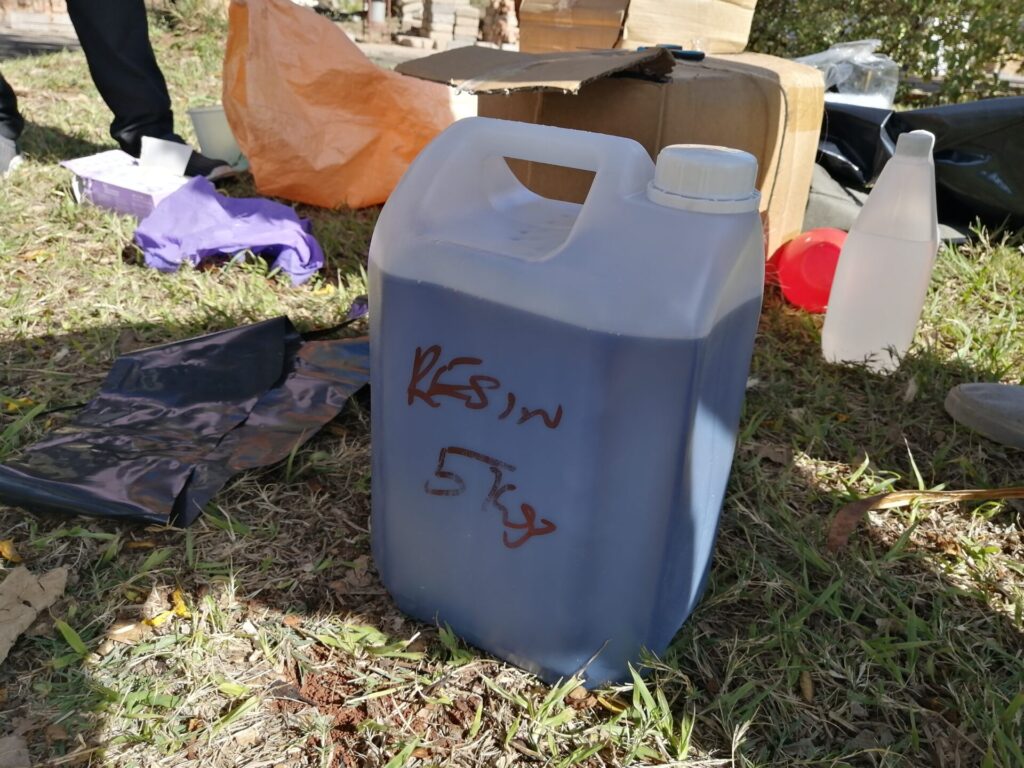
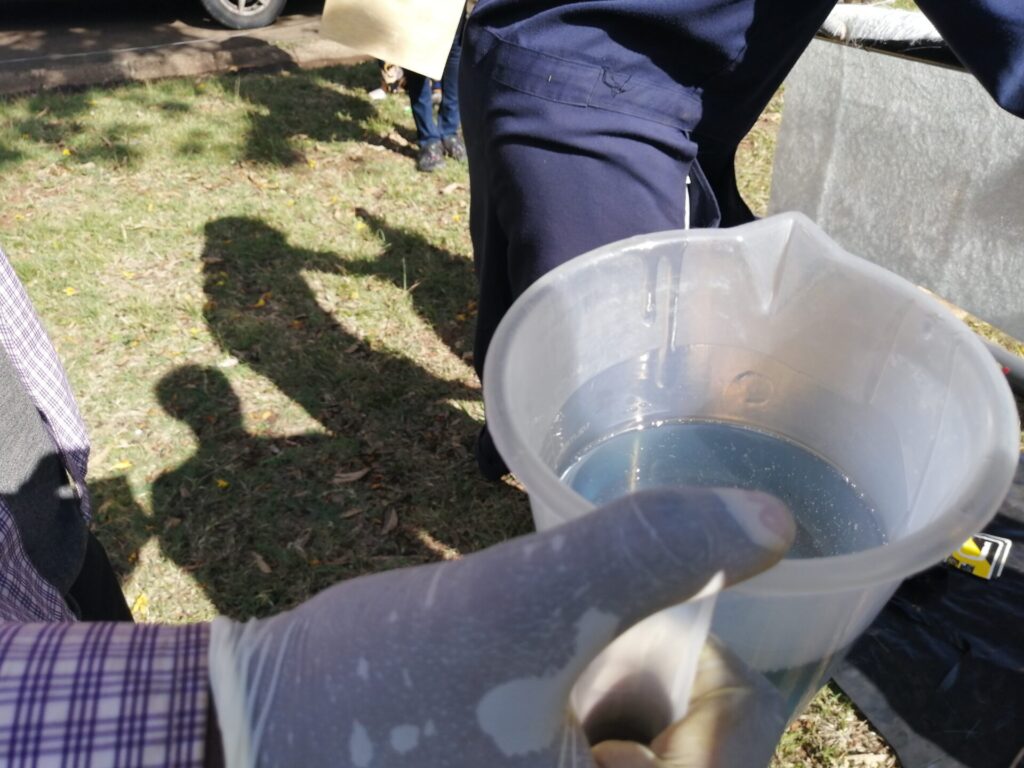
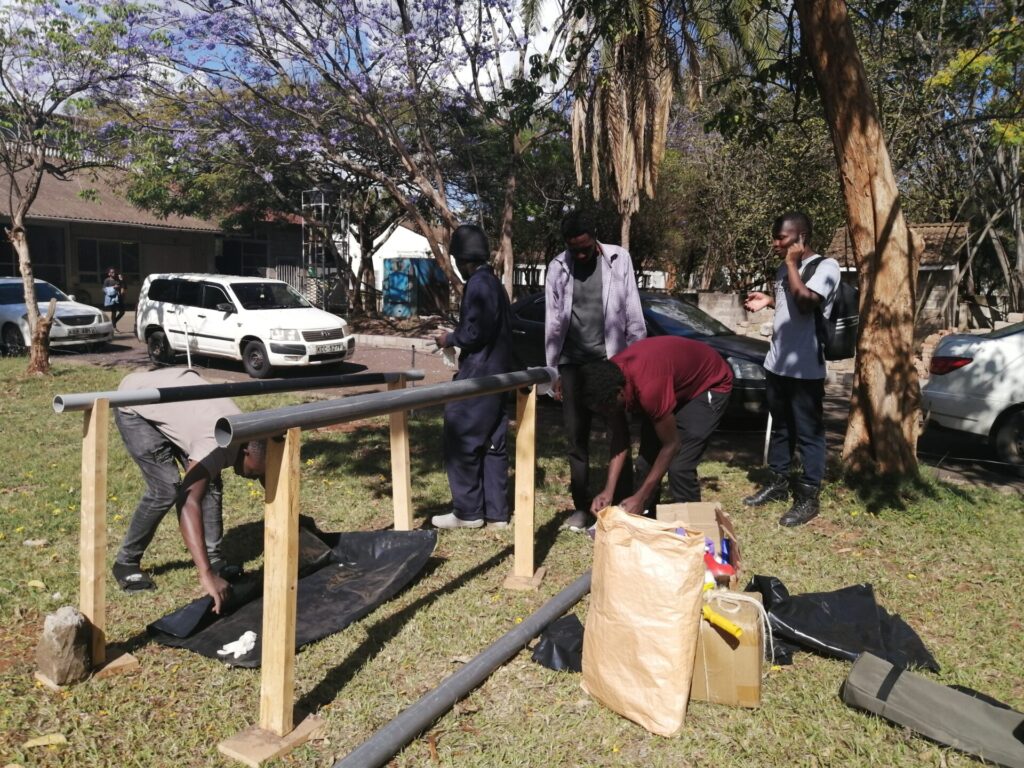

Improvement of solid motors and testing of recovery mechanisms
I have previously blogged about the N-2 rocket’s improved solid motors.
Since the aluminum combustion chamber melted in the recent test, the static test had to be conducted with the combustion chamber changed to mild steel. I was just in Japan on a business trip, but under the supervision of my colleague, the students were able to successfully conduct the test.
In the video above, the test stand is plodding along, and this was caused by the bulkhead coming loose from the rocket motor. The bulkhead came off because the groove in the combustion chamber that stops the snap ring to secure the bulkhead was too shallow. The following test was conducted to improve on this point.
The thrust curve is shown below, with a peak thrust of 514 N recorded. This time, the nozzle, not the bulkhead, was ejected, resulting in a rapid pressure drop. Next, the nozzle side was also tested with a deeper groove in the snap ring.
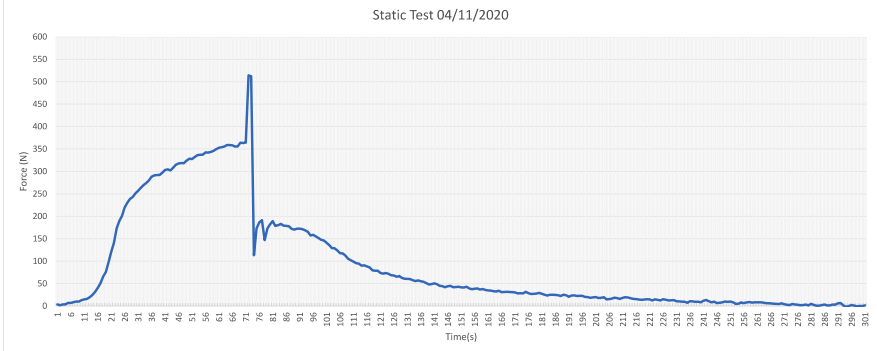
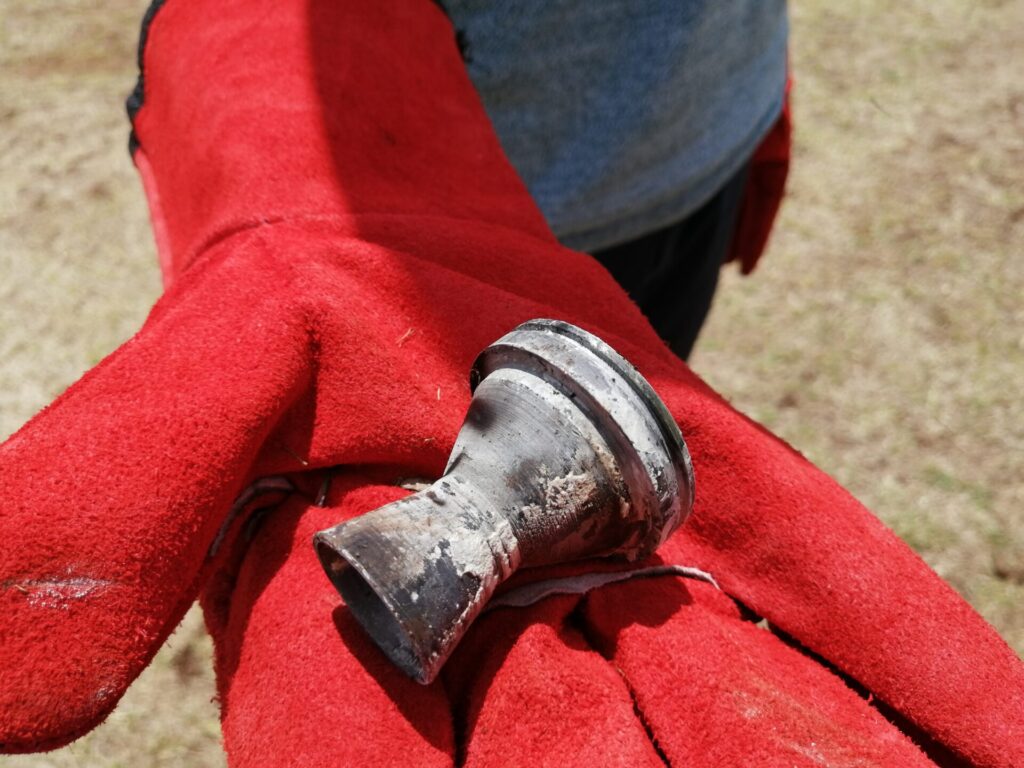
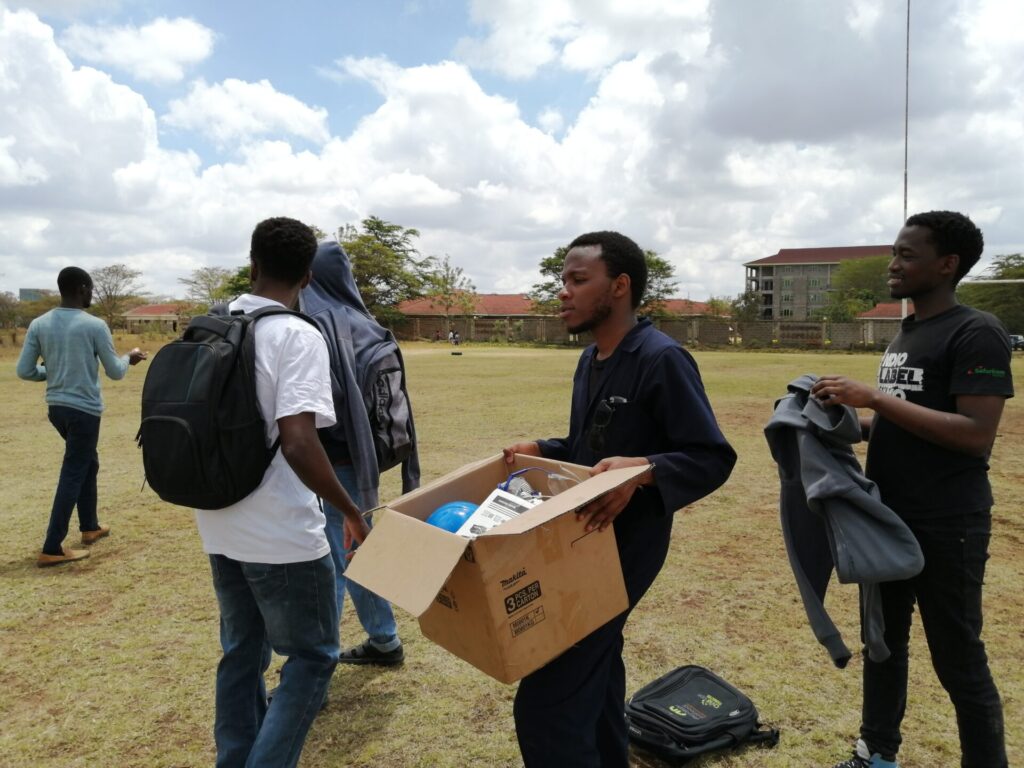
Now, in addition to the improvement of the solid motor, another important thing is the recovery mechanism, i.e., the recovery of the rocket by parachute. Unfortunately, the recovery by parachute has not been successful so far, and it is a long-cherished goal to achieve it in the next launch of the N-2 rocket. The ejection of the nosecone uses pyrotechnics, specifically an explosive called crimson powder.
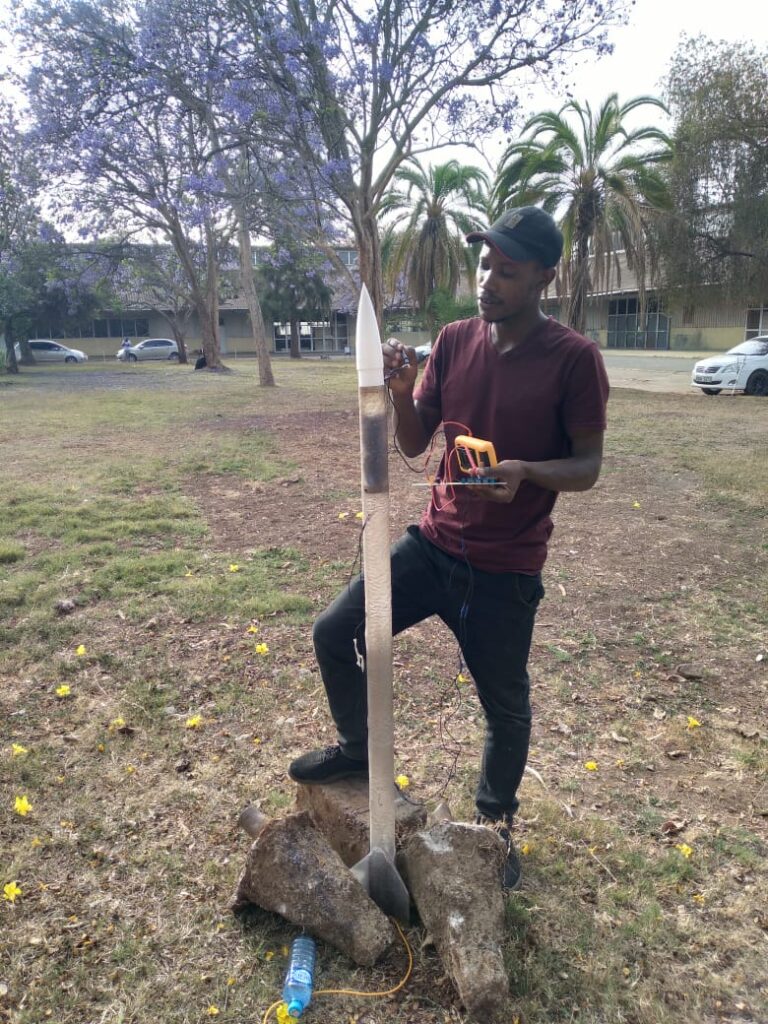
In addition, to test the control program (state machine) implemented in the flight controller, the team built a water rocket for the experiment.
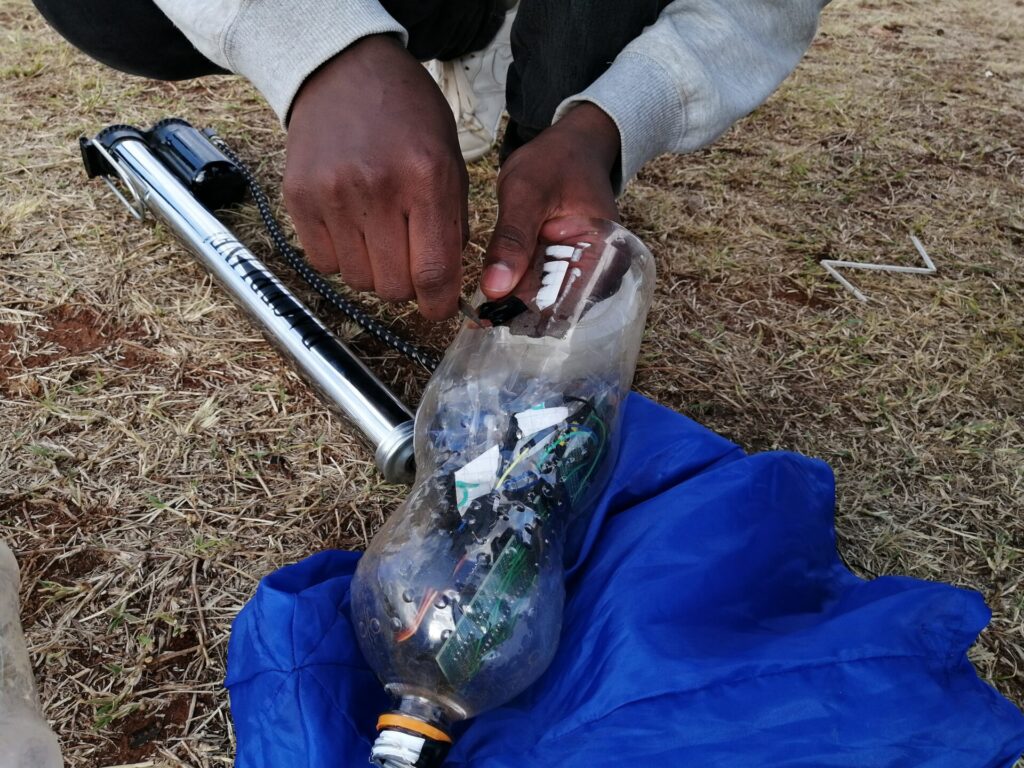
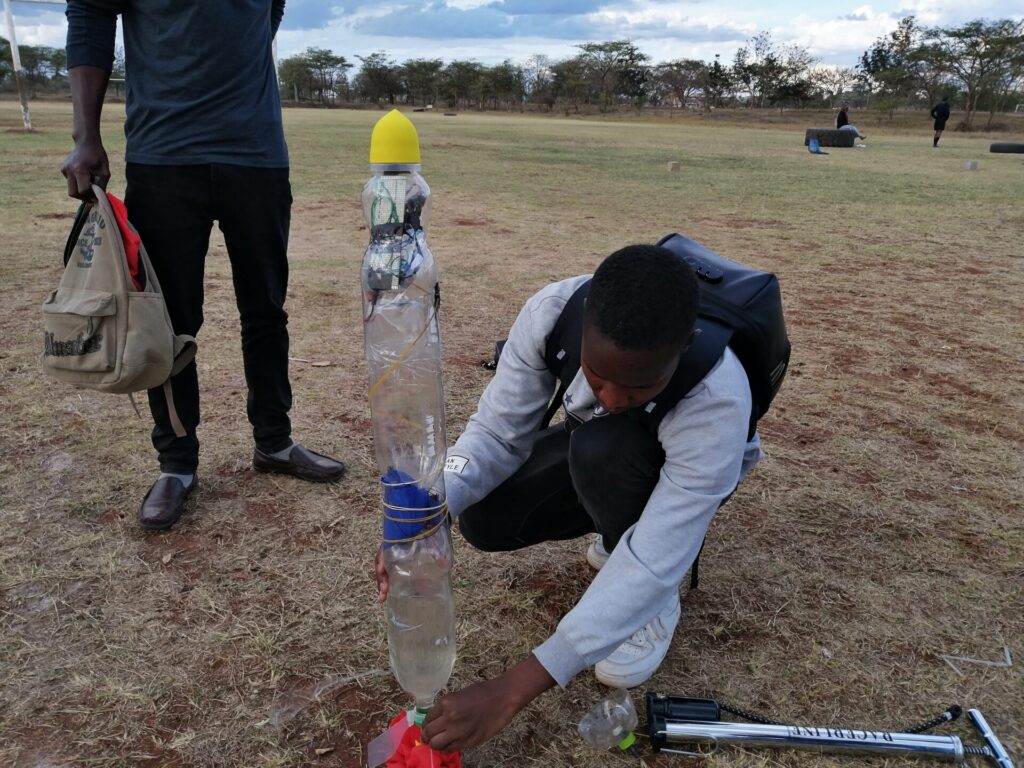
Water rocket launch (success)
Visiting Japan with JKUAT Students
I visited Japan with 10 JKUAT students and 5 JKUAT faculty members. The students were invited by the Tokyo City University as part of an exchange program called Sakura Science, which is implemented by the Japan Science and Technology Agency (JST). The students stayed in a laboratory working on robot and drone control, and conducted experiments in a research environment that they could not experience in Kenya.
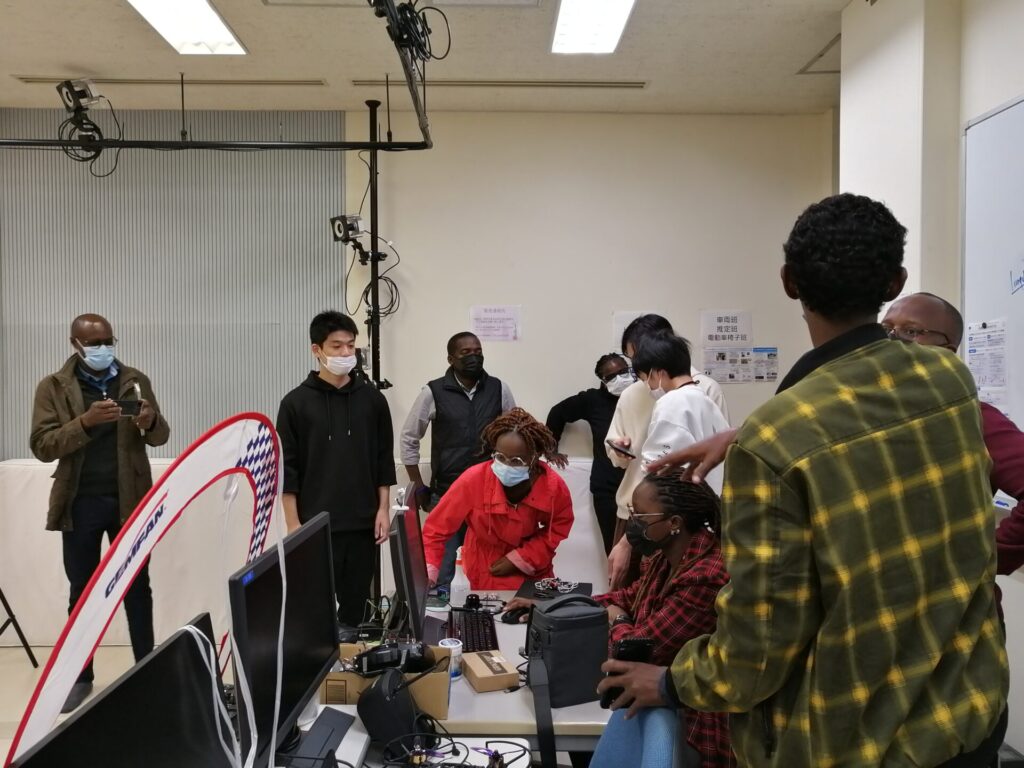
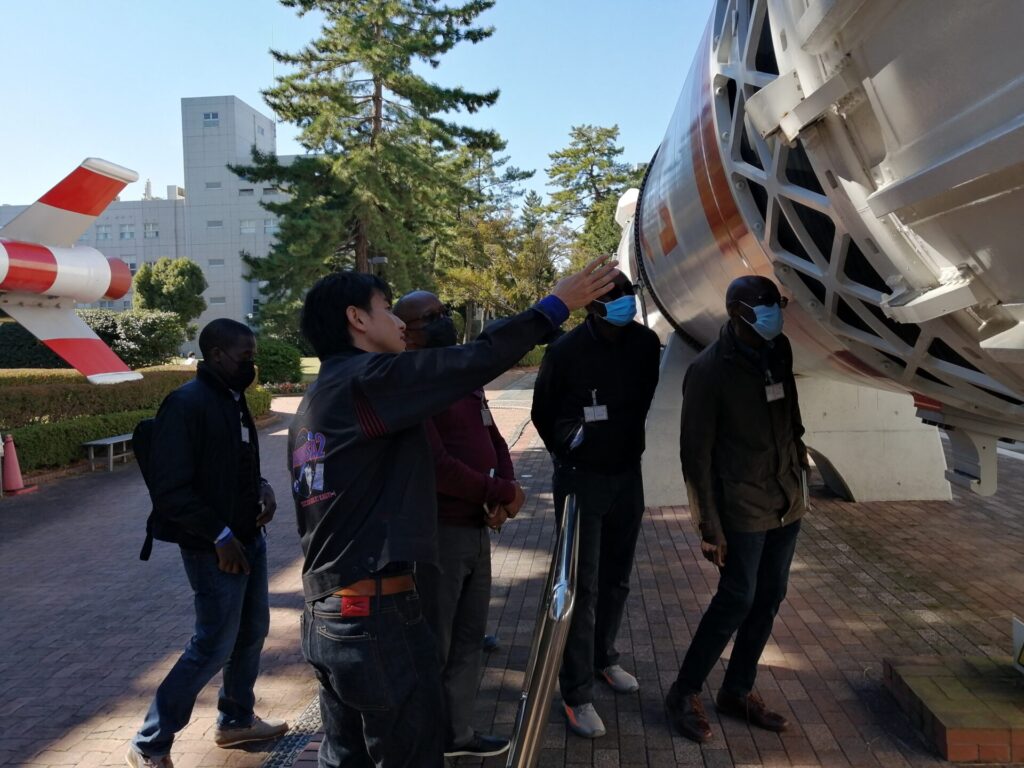
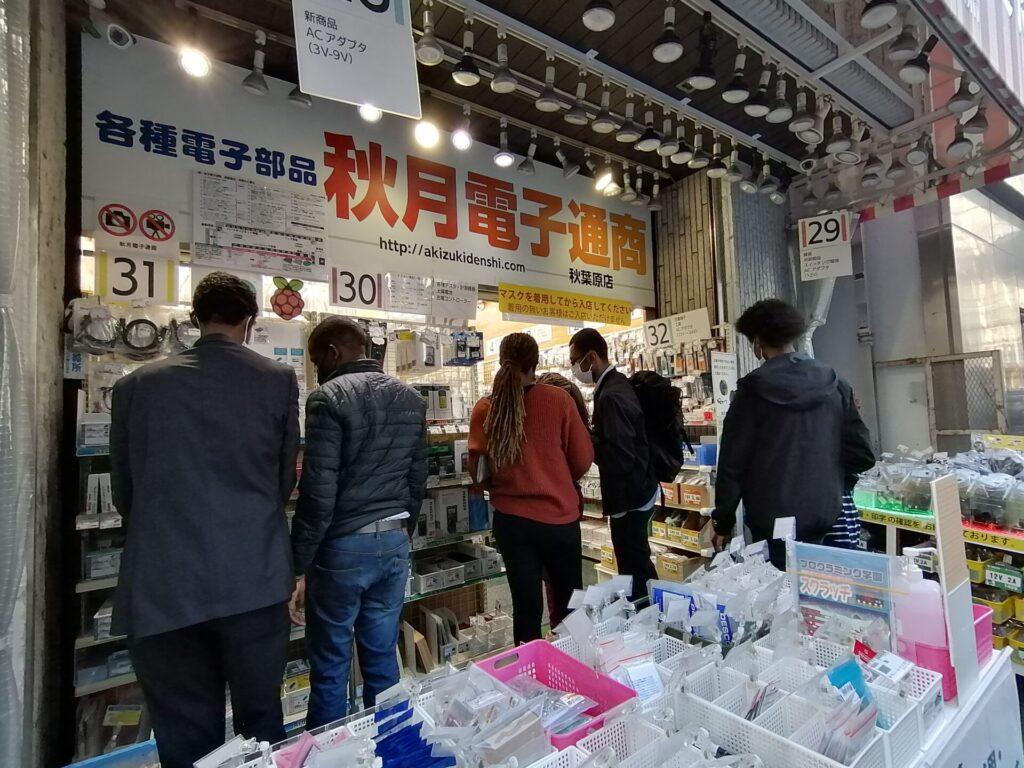
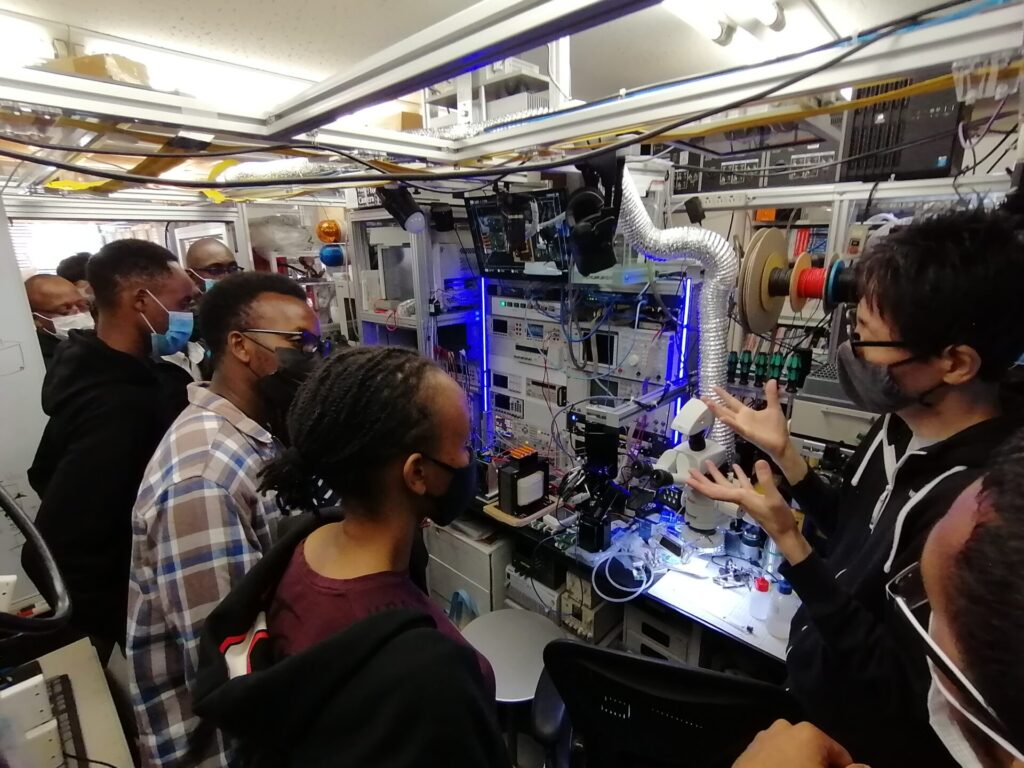
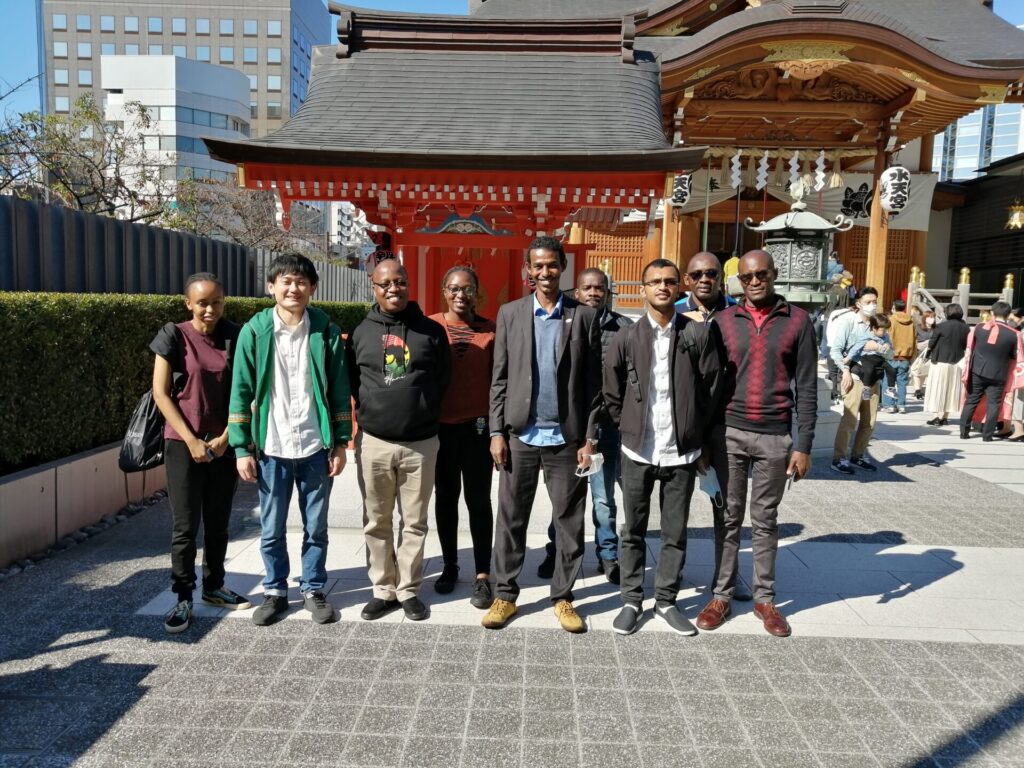