Leading up to the Robotic competition at JKUAT
About
Time goes back to 2019. I observed a robotics competition called Roboken, organized by the Kenyan Ministry of Education for vocational training schools (TVET). This robotics competition has been held for the past several years and I heard JICA was involved in the beginning.
Nagasaki University professors were involved in this Ministry of Education robotics competition as judges, sitting at the judges’ table set up in the hall of the convention center (KICC), where the event was held. Although the robots developed were small in scale and simple in function compared to those in Japan’s technical college robotic competitions, it was wonderful that each school worked as a team and the competition was systematically managed by the Ministry of Education. It led me to think about whether a similar activity could be done at JKUAT.
Many students at JKUAT are interested in the field of robotics, and many are working on agricultural robots (seeding robots, lake weeding robots, drones, etc.) for their final year projects. Although some faculty members are interested in researching robots, I felt that there are few who focus on robotics itself as a research subject.
In fact, when I was thinking about coming to Kenya, AI-based agricultural robotics was one of the fields I wanted to work on. After I arrived in Kenya, I decided to start a research group on robots in JKUAT, based on my experience to supervise a PAUSTI student working on an agricultural robot (a robot that diagnoses diseases from images taken by deep learning) and to teach a graduate course on robotics at JKUAT. In April 2021, I asked my colleagues who might be interested, such as faculty members in mechatronics, computer science, electrical and electronics, etc. Since they expressed interest, I decided to start the activity. The group decided that the main activities of the group would be to organize robotics competition and to train students on the knowledge and skills necessary for robotic competition. The idea was finalized in January 2022.
The program was called Robotics Dojo, and the first step was to recruit students to participate in the program. 25 students were expected to participate in the program, and 43 students were actually accepted. The program is divided into two parts. The first part is technical training, in which students learn the technology required for the robotics competition over a period of three months starting in May. The second part was robot development for the actual Robotics competition. The initial plan was to hold the Robotics competition in October 2022 and invite the Japanese Ambassador to Kenya and high-ranking officials from the Ministry of Education to participate in the event on a large scale.
Robotics Dojo begins
Although the kickoff meeting with the students was held at the end of May 2022, the operation of Robotics Dojo did not proceed as initially envisioned. The biggest obstacle was the design of the robotics competition, i.e., what the content of the contest would be. Neither myself nor my fellow JKUAT faculty members had any experience participating in robotic competitions. Even if we were to refer to other robotic competitions in Japan, there are many well-known ones, such as the National College of Technology Robocon, NHK Robocon, Robocup, and Kawasaki Robot. To determine the topic for our robotics competition, we needed to consider some kind of criteria. The following criteria were considered in determining the content of the robotics competition.
- Agricultural robotics. Agriculture is a major industry in Kenya, and the impact on the audience and media will be significant; since JKUAT is an agricultural and engineering university, it will also help improve the brand of the university.
- The competition should be interesting and enjoyable to watch. It is even better if the content is media friendly.
- Robots that show promise for commercialization are preferred. It can give the impression of contributing to Kenyan industry.
I wanted to get ideas freely from students, so we held a brainstorming session with a group of students. The students came up with ideas such as a harvesting robot and a spraying robot, but they were not conclusive ideas. Later, while searching the Internet for agricultural robot contests, I found a university in Texas or somewhere that had a robot that harvested cotton models as its subject, and I thought this was it. I thought it would be a good idea to modify this robot in the Kenyan context, and came up with the idea of a robot that would use image processing to locate the fruit (tomato or strawberry) from a camera image and harvest it with a robotic arm. However, this idea was rejected because it seemed boring to watch.
As the ideation began to be stuck, I called up a group of students who were working on rocket development and discussed it with them. As a result, we came up with the idea of putting aside the issue of agriculture and competing for overall points by tackling a variety of issues, in a format similar to a “Makunouchi bento lunch box”. In fact, instead of focusing on the domain of agriculture, I felt that it would be better to focus first on the technical challenges and then decide the content of the competition. The significance of the challenges (i.e., what are they useful for?) should be decided later. As a result, we devised a competition that combined line tracing (robots move along black lines) and pick-and-place (robots move objects to designated areas according to their colors). This idea was also heavily influenced by the ET Robocon, a contest combining line tracers and assignments, which I happened to find on the web at the same time.
Having decided on a general idea, I started to actually implement it and check the difficulty level of the competition. For line tracing, I bought a robot kit and implemented PID control by myself. For pick-and-place, a complex process is required to determine the object’s color using a color sensor, identify the destination for moving the object using a camera and image processing, and calculate the sequence of the movement path (e.g., one step forward, turn 90 degrees to the right, two steps forward, etc.). I simulated the path generation in Matlab and implemented it on an Arduino, but found that it was difficult to get it to work properly due to the large influence of mechanical errors. I also tried to put together a simulator using Unity. I had planned to have students use it, but in the end I did not use it because the content of the competition had changed.
After further consideration, I concluded that pick-and-place was too complicated and removed it from the tasks. Meanwhile, a strong request came from a student to include a maze as one of the tasks. I searched maze solving robots to see how it’s difficult, and I was shocked when I saw a video of Micromouse. The micromouse moved so fast and looked cool. I felt that it was a task worthy of targeting. In addition, the engineering student group at JKUAT had recently held a robotics competition targeting mazes, and I felt that there would be synergy.
The competition proposal was not finalized until late September 2022. Once the task was decided, all that remained was to create the gamefield.
Gamefield design and fabrication
I designed the gamefield using Fusion 360.
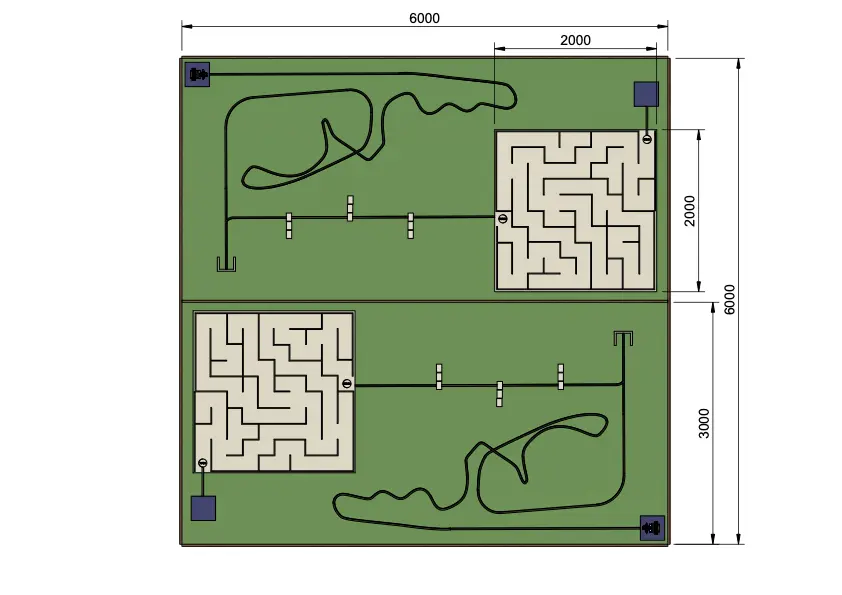
The whole is divided into four parts: 1) complex line tracing, 2) stop-and-go (parking), 3) obstacle avoidance, and 4) maze.
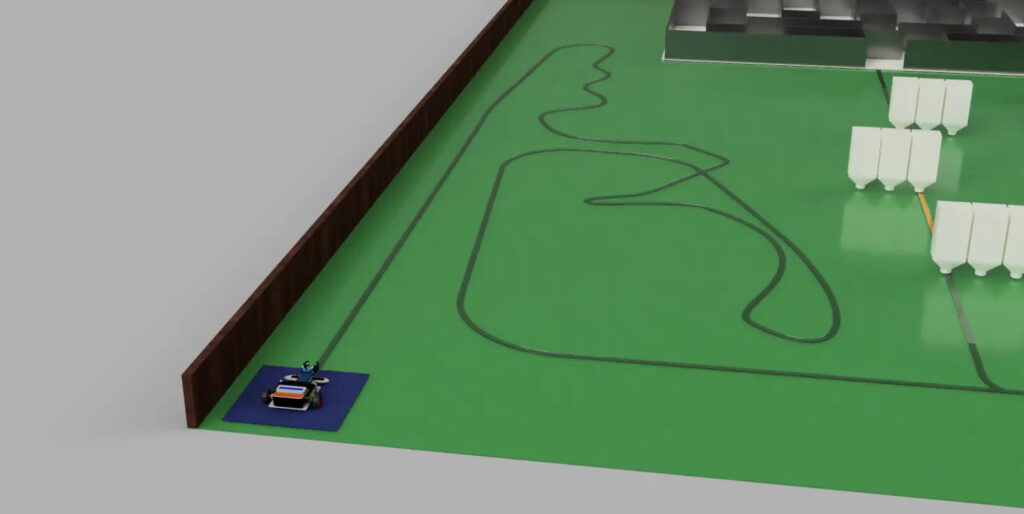
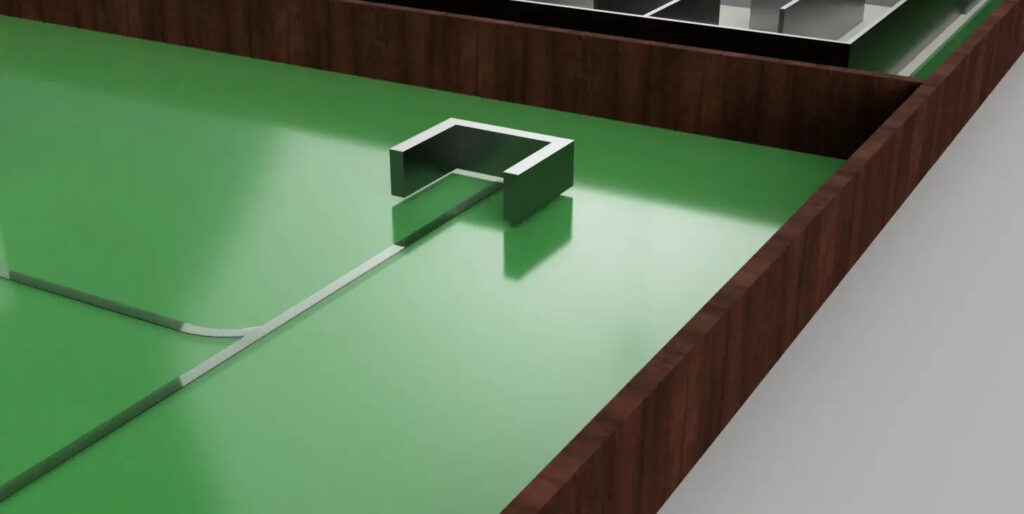
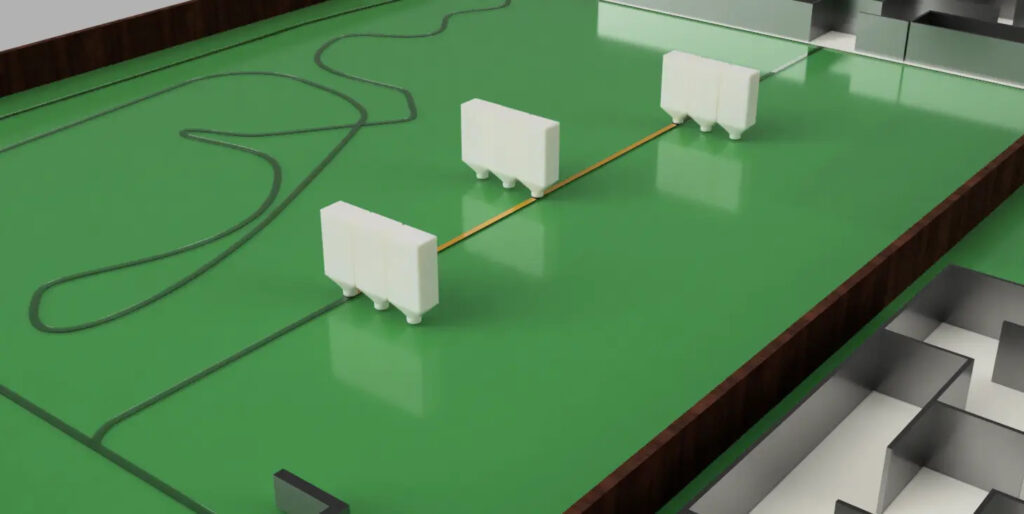
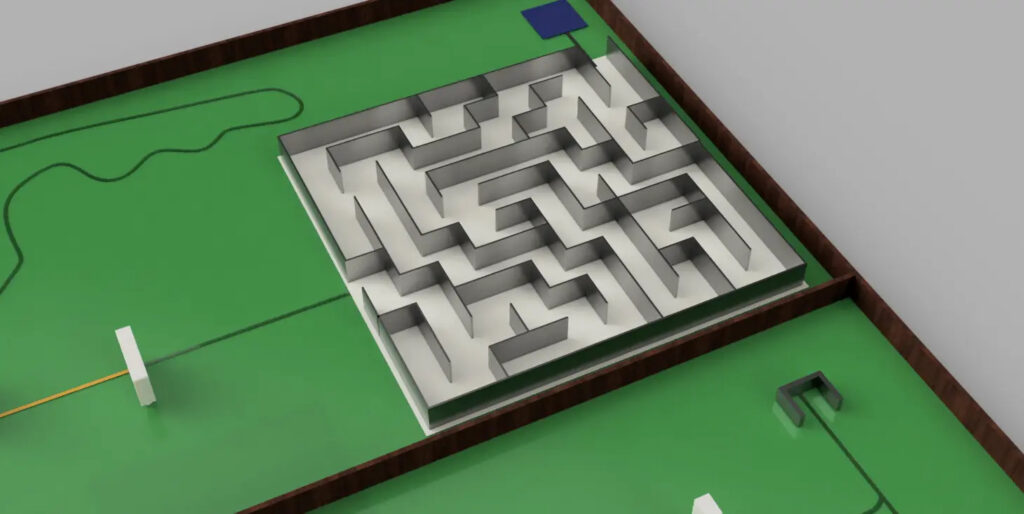
In creating the gamefield, it was desired that the gamefield could be set up freely at any location for practice, so folding and storage were taken into consideration. For this reason, the field was made of vinyl floor mats (material used for banners), and black lines for line tracing were attached using standard size vinyl tape of 19 mm width. For the maze, we used a combination of wood panels, and for the obstacles, I collected milk bottles.
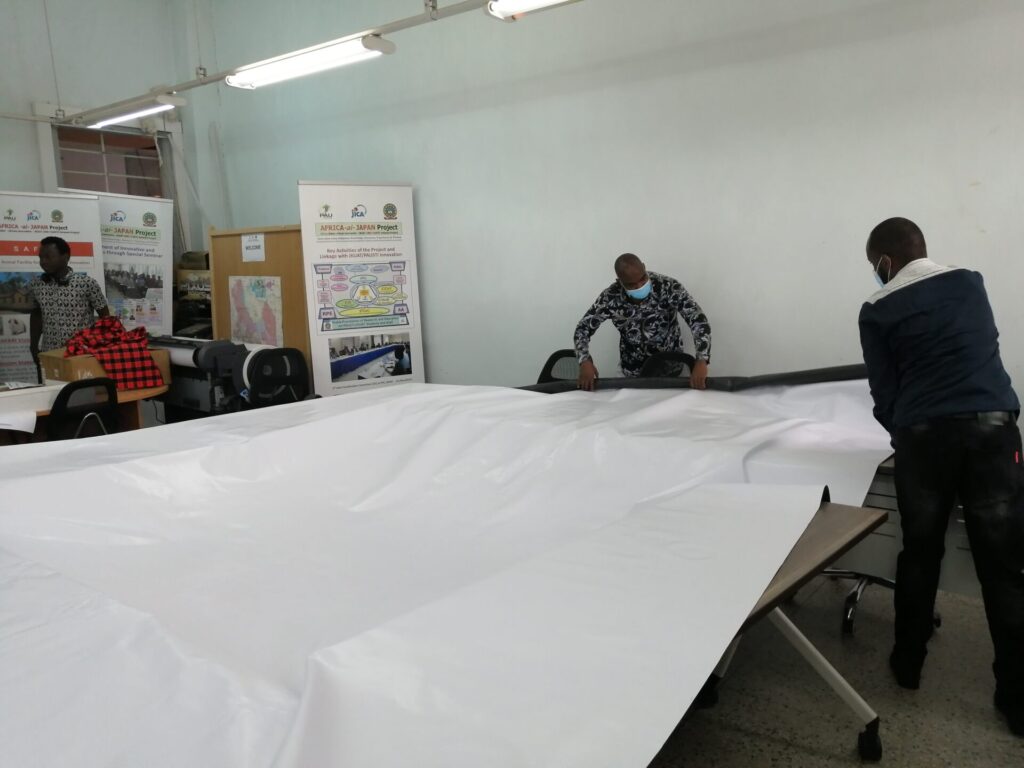
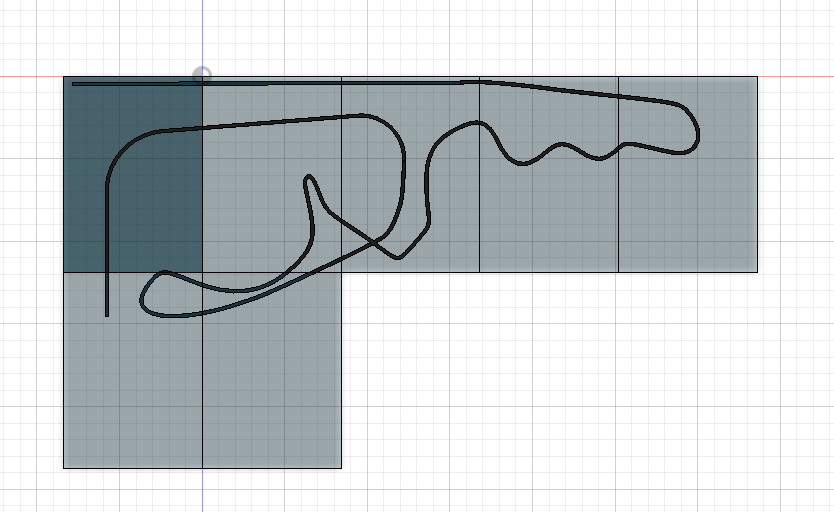

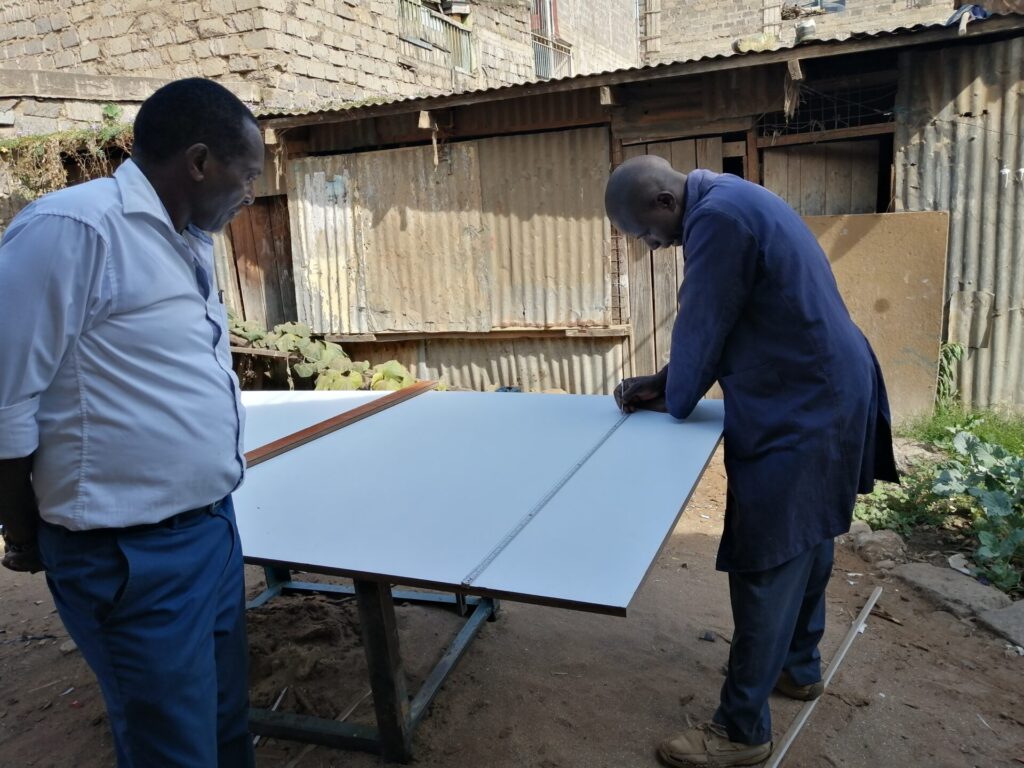
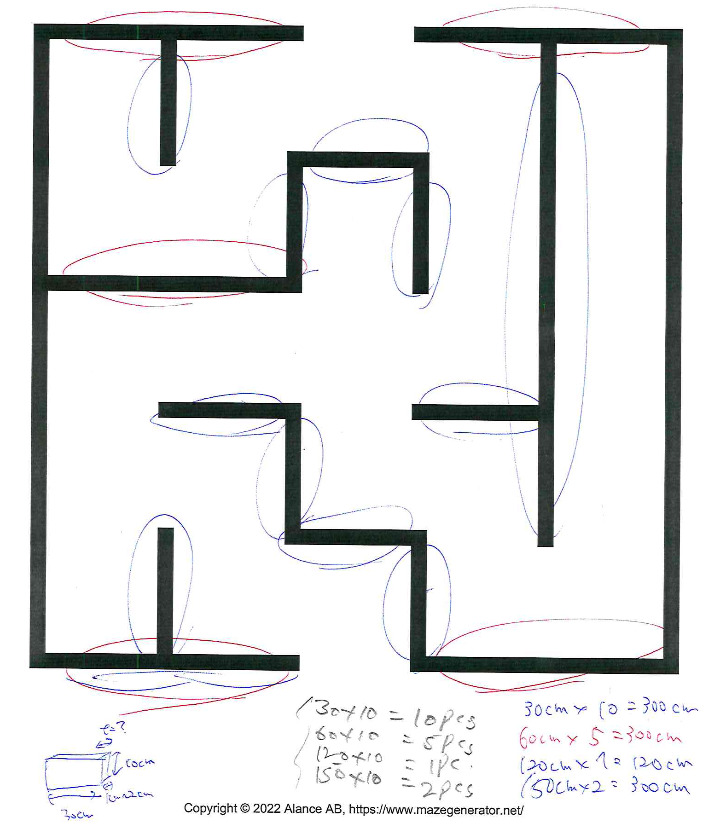
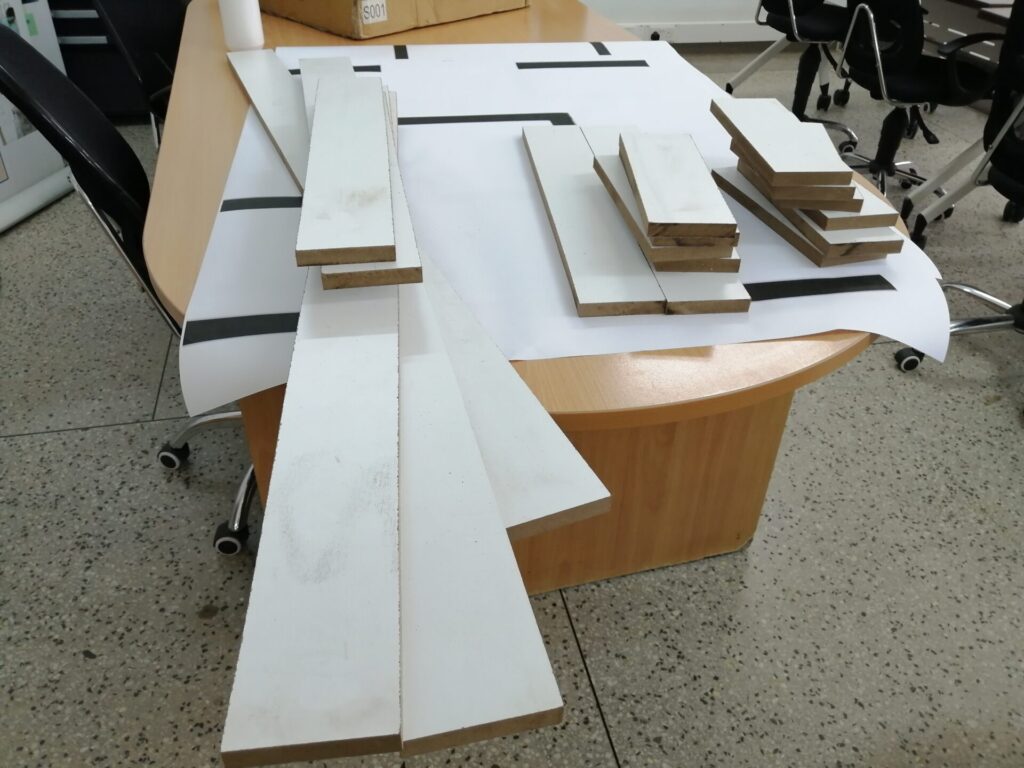
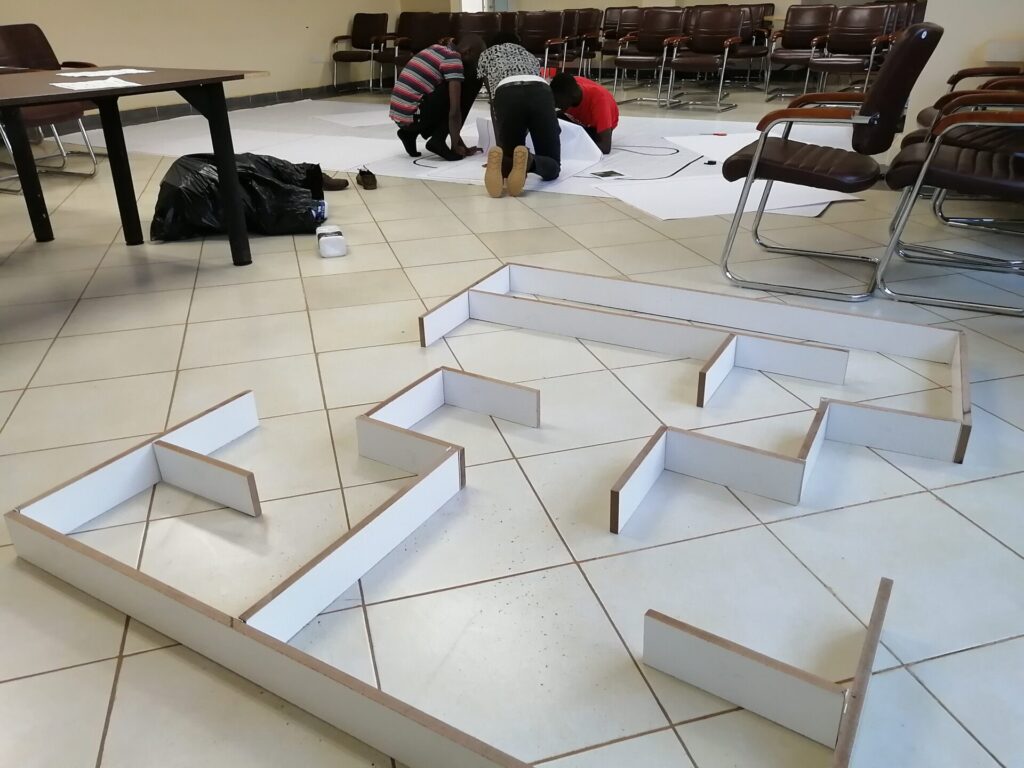
Support by Nagasaki University professors
The Ministry of Education’s robotics competition was not going to be held due to COVID-19, but by chance I got in touch with some professors from the Faculty of Engineering at Nagasaki University, who had been involved in this robotics competition for many years. When I discussed the idea of holding the robotics competition at JKUAT with the professors of the Faculty of Engineering, they readily agreed to support the event. Initially, we had planned to have them participate as judges for the robotics competition, but due to delays in planning, I decided to ask them to provide advice and technical guidance on robot development instead of serving as judges. As it turned out, this change was a good decision, and the students were very satisfied.
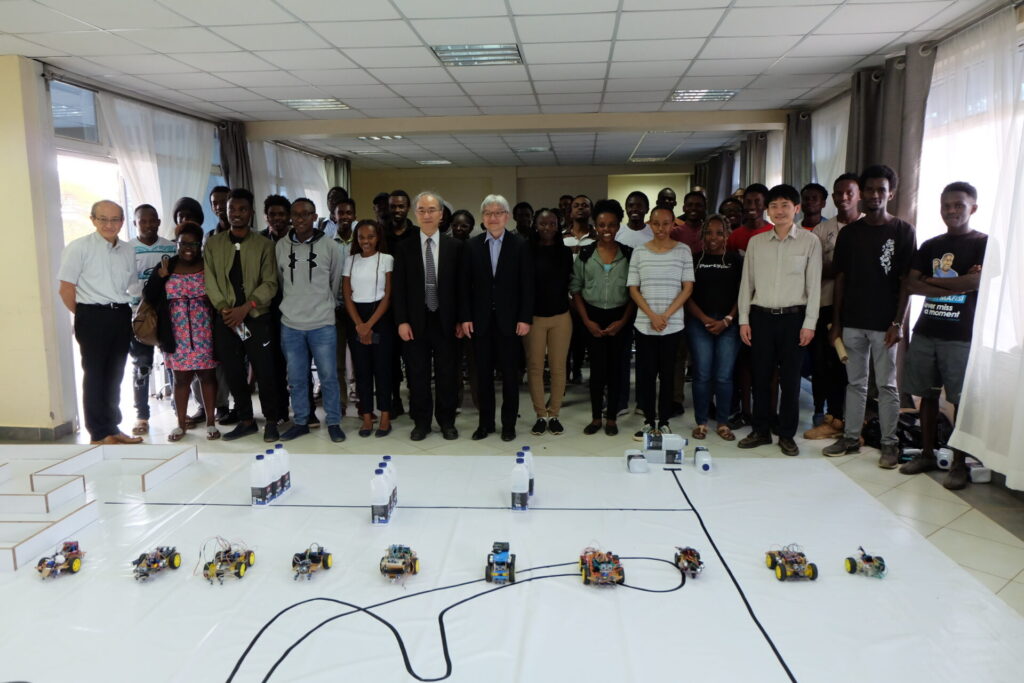
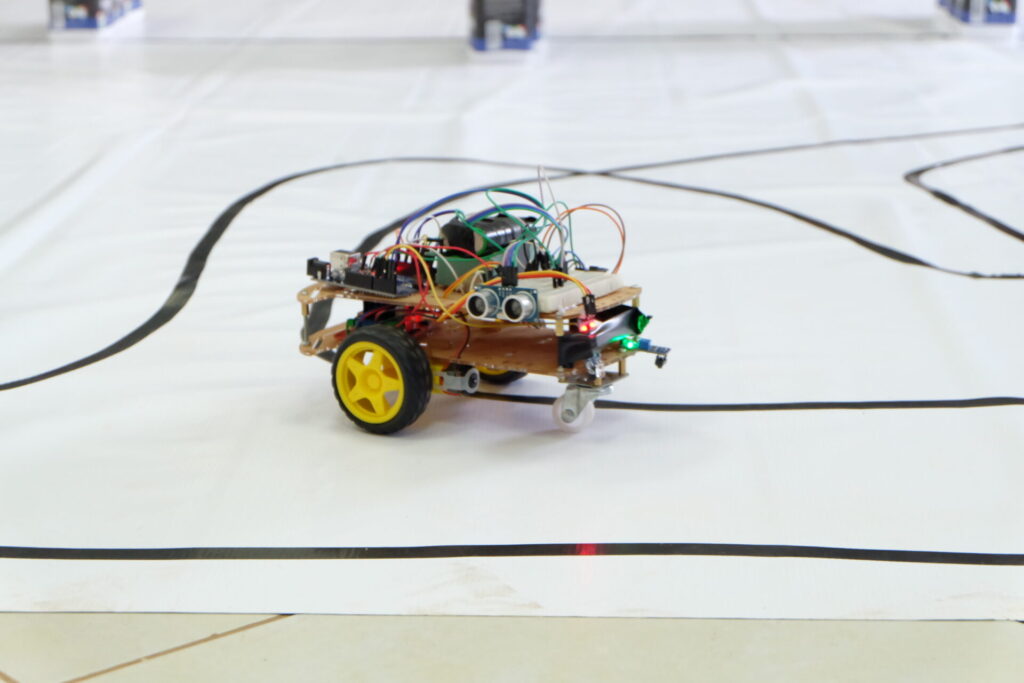
About the future
The actual robotics competition is planned for mid-November (this month). We would like to expand the event outside of the university after next year, but we need to think about how to do go about it, including the management structure.
P. S. The final competition was covered by a newspaper in Kenya.
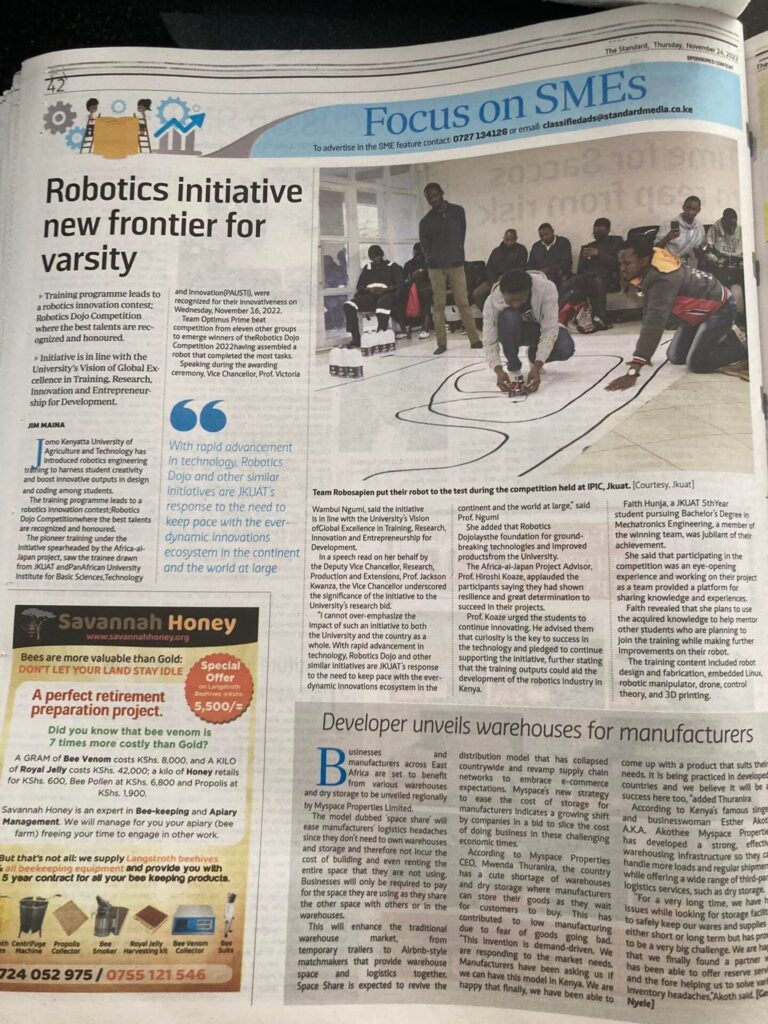
Inverter test/improvement of propellant
Regarding the N-2 rocket under development, the planned launch this Tuesday has been postponed due to circumstances. As for the future, KSA will conduct a one-time location scout in Isiolo, and then the the contact person will get back to us with a convenient date.
Today, the inverter arrived as a power source for outdoor use, and we checked its operation with the support of the technician in the electrical laboratory.
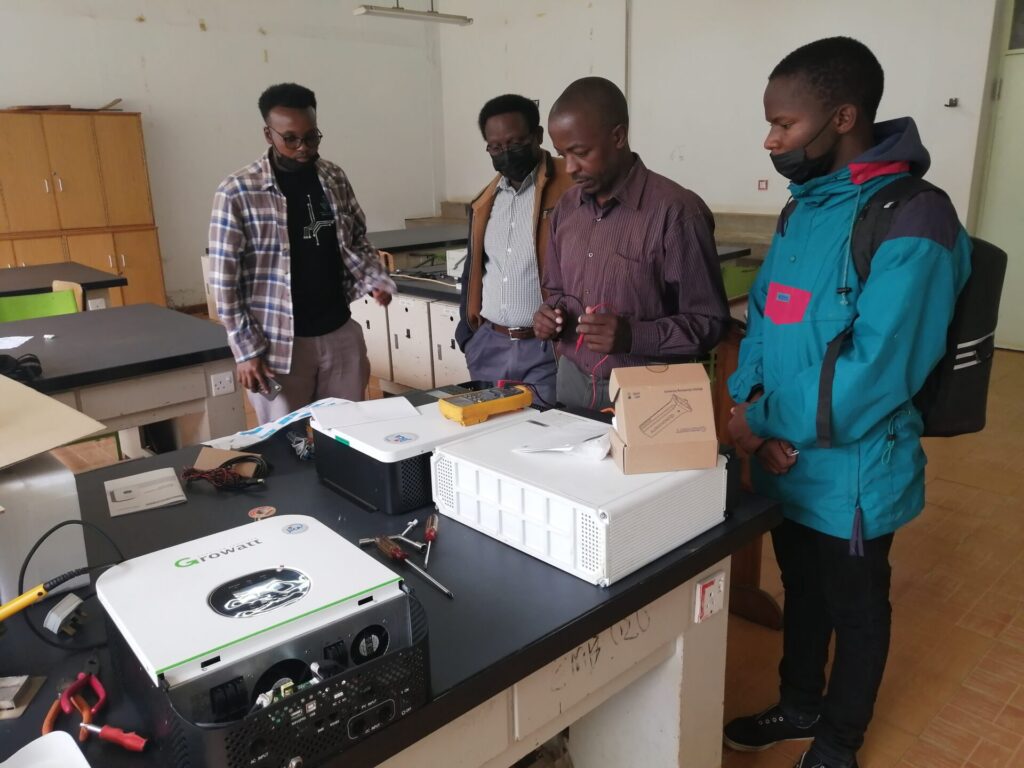
After returning to my office, I received a phone call from a student in the propulsion group. He said that he had accidentally ignited the propellant when he was making it, and that a lot of smoke was coming out. I told him I was on my way and found the engineers evacuating outside the building.
I rushed upstairs and found about four students who had been working on the production. When I asked them what happened, they told me that when they were pouring the propellant into the combustion chamber, the spilled propellant came in contact with the heater and ignited the propellant. Fortunately, no one was injured and no fire broke out, and only smoke was generated.
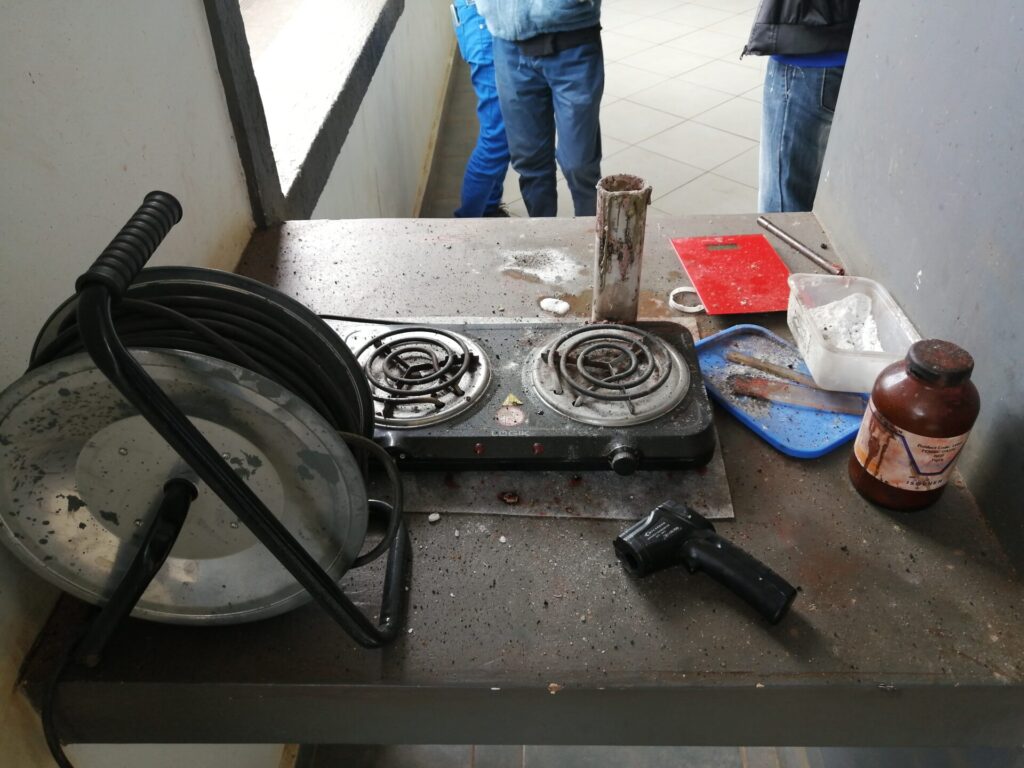
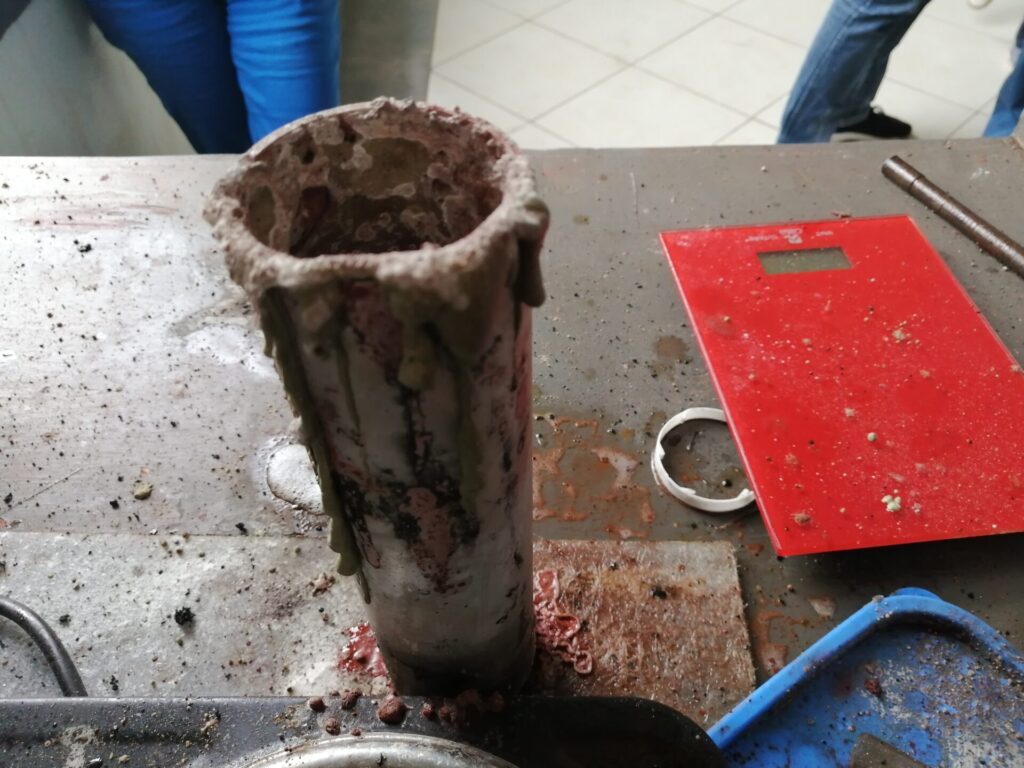
The team then discussed and discussed how to respond to the lessons learned from this incident. As a result, the following improvements were implemented
- Casting outdoors
- Inform workshop manager before casting
- Increase the size of the pan (to prevent leakage during heating)
- Use of induction heaters (not to expose heating elements)
As a fellow faculty advisor commented, as we move forward with the development of liquid rocket engines in the future, we need to take even more safety measures and raise safety awareness.
Development of Jibebe 2nd model begins
After completing the first electric tricycle, two students from the electrical engineering department wanted to work on a second model for their final year project. Today, the students visited APDK, an NGO that manufactures and sells tricycles for people with disabilities. APDK kindly agreed to donate a tricycle for us to develop our second model. We are looking forward to the future development of this project.
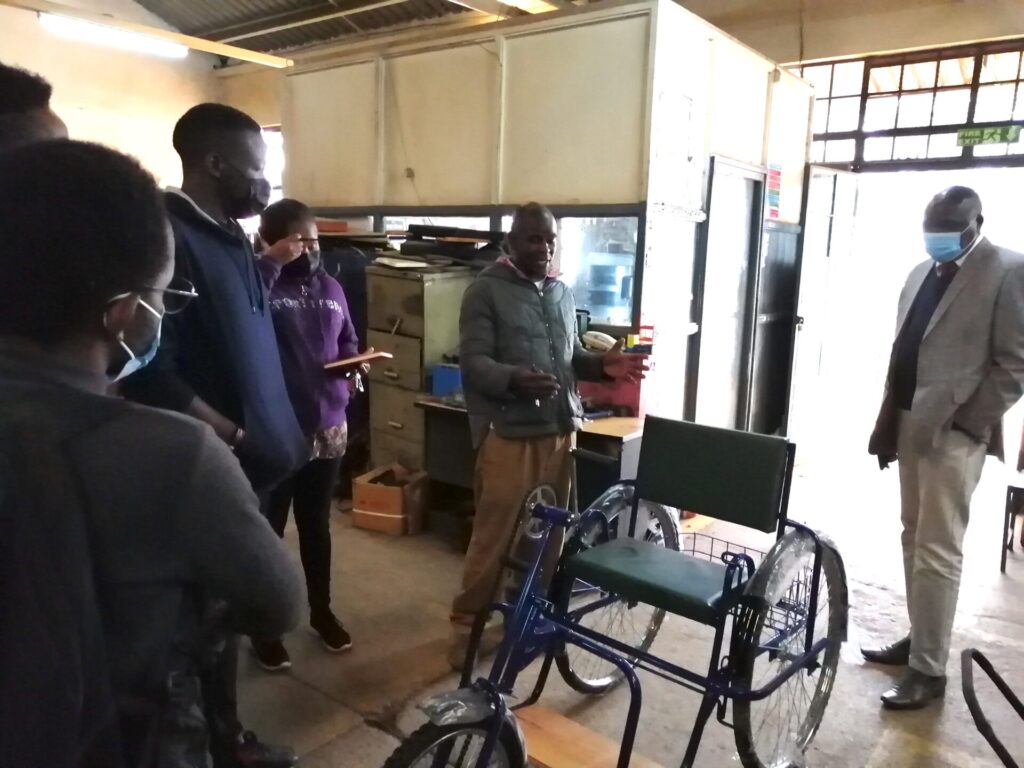
Setting up Tripoli’s Kenya Chapter
There is an international model rocket organization called Tripoli. At the recent Space Expo, an engineer from the U.S. suggested in a panel discussion that we should establish the first Tripoli branch in Africa in Kenya. He said that he needs Tripoli members to open a branch, and he is willing to help us with that. He introduced students from the University of Nairobi who are interested in this idea. We will have a kick-off meeting tomorrow at JKUAT. We are hoping that this will open the door to university students and high school students from outside JKUAT as well as to alumni.
Full grain test with modified mild steel nozzle
Preparations are underway for the launch of the N-2 rocket. The schedule has not been decided yet, but we are working with KSA for mid-July. Today, the propulsion team conducted a static test. It was a solid motor test using two grains, the same as the one used in the main test.
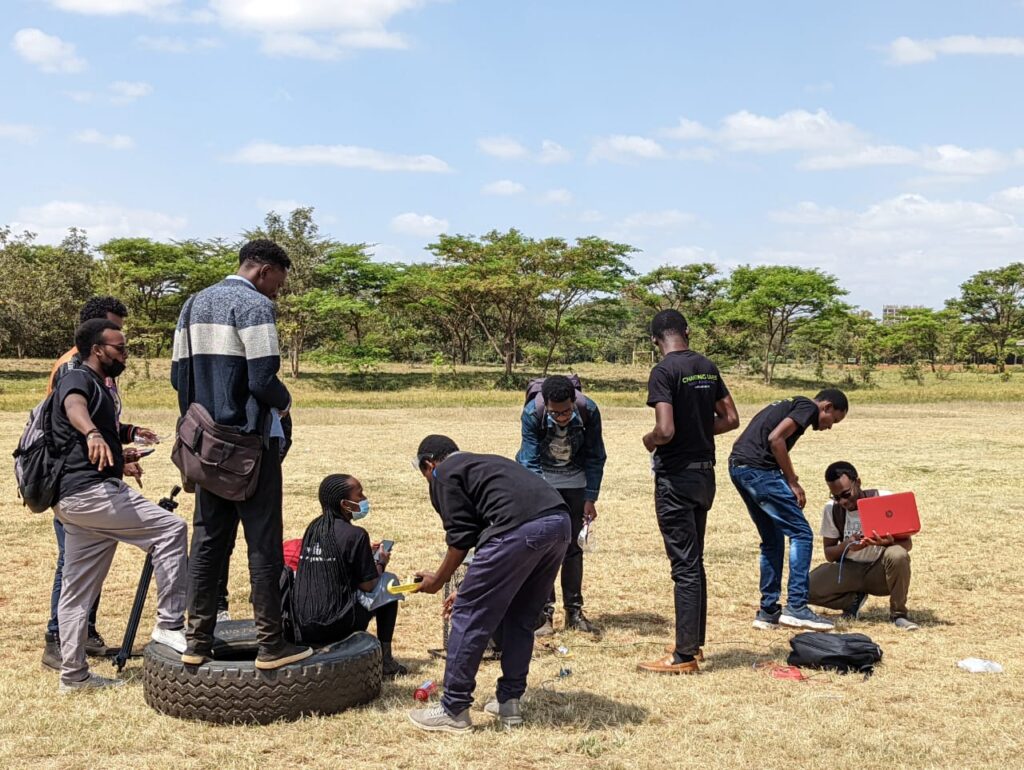
Unfortunately, I had a meeting and could not be there. I was shown a video later and found that the side wall near the end cap had melted, causing the gas to blow out in the middle. The nozzle also melted last time, but this time it was safe because we changed from aluminum to mild steel.
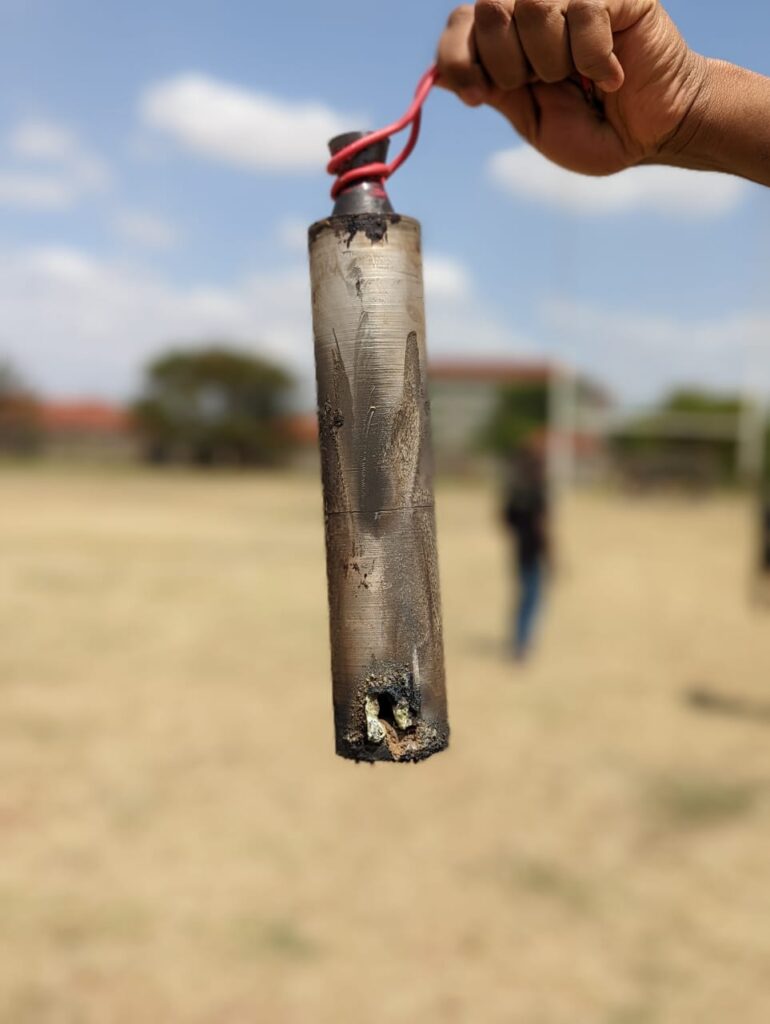
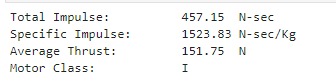
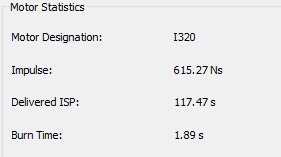
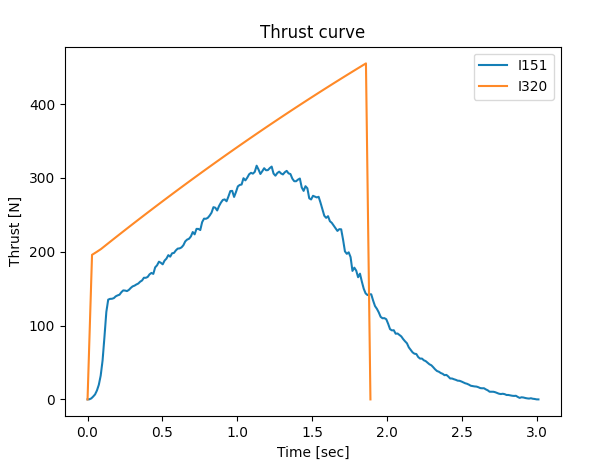